The reason why welding machine lasers are easily damaged.
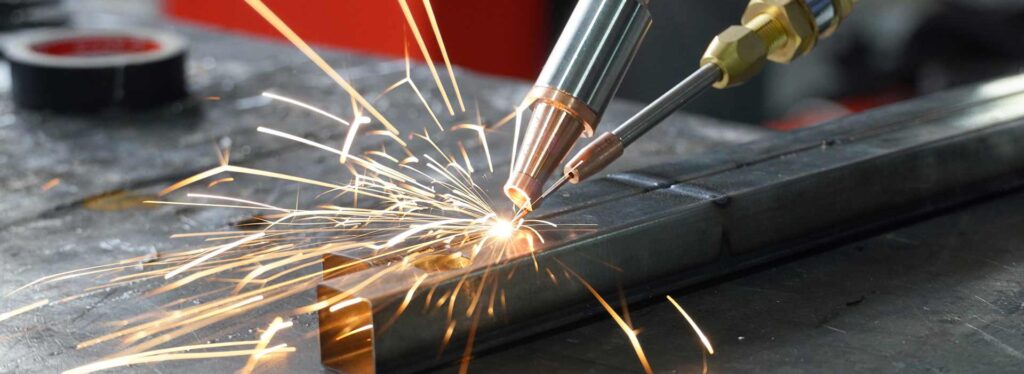
The laser cutting process uses high-power and high-density laser beams to scan the surface of the workpiece and locally heat the material to thousands or even tens of thousands of degrees Celsius in a very short time, so that the irradiated material can quickly vaporize and melt. , ablate or reach the ignition point at the same time, the molten material is blown away by the high-speed airflow coaxial with the beam, so as to cut the workpiece and achieve the purpose of cutting the material. At present, the purity of compressed air in large domestic steel plants often cannot meet the high-precision requirements. This is one of the main reasons why the light guide system in the output mirror of the laser welding machine is often contaminated. In addition, peripheral water cooling is currently commonly used to cool the output mirror, and its failure modes are reflected in thermal damage and thermal deformation. The thermal deformation caused by the absorption of the anti-reflection coating on the inner surface, the anti-reflection coating on the outer surface, the base material and the lens surface will have a huge impact on the output beam quality, and in severe cases may even cause damage to the output mirror. Under high laser power density, the output mirror cannot dissipate the heat it absorbs, causing the temperature to rise continuously. The absorption further increases, causing the temperature of the substrate to further rise. Under repeated cycles, the laser output mirror may break due to excessive thermal stress. Because the temperature of the laser output window transmission mirror is too high and the central part expands too much, the central part will bulge and deform. Since the central intensity surface of the laser beam will gradually weaken toward the edges, the light intensity distribution within the beam cross section is not very uniform, which will lead to poor heat dissipation conditions in the center and uneven expansion of the lens everywhere. Because the lens material has a positive refractive index and temperature coefficient, it will produce an effect like a convex lens, which will greatly reduce the service life of the laser output mirror of the welding machine.
Thermal lens effect of laser output mirror
The most commonly used in high-power lasers are ZnSe (zinc selenide) output mirror and the YK52 laser cutting head of a German company. The YK52 cutting head has a larger lens with a diameter of 52mm, making it suitable for lasers with lower radiation quality or higher power. Thanks to the long collimation focal length and focusing focal length, the laser focal length can be optimally adjusted. The main source of pollution on the outer surface of the laser output mirror is dust in the air, and the main source of pollution on the inner surface is the sputtering of cathode discharge and the medium in which the laser works. Both types of pollution are random and non-universal. According to the equipment instruction manual, under the action of high-power CO2 laser, the center temperature of the ZnSe lens is the highest, the water temperature is maintained at the junction of the periphery and the water-cooling jacket, and the temperature of the outer surface is much lower than the inner surface. Through field test data, it was found that the thermal deformation of the ZnSe cavity piece is directly proportional to the laser output power, the absorption coefficient of the high-reflective film and the thermal expansion coefficient of the substrate itself, and inversely proportional to the thermal conductivity of the base material and the transmittance of the cavity piece. There is no correlation between the light transmission radius at the center of the ZnSe lens and the amount of thermal deformation. The thermal deformation of the lens will increase as the power density increases as the spot diameter becomes smaller. Relatively speaking, the cooling conditions at the center of the lens will be improved because the radius of the peripheral cooling water jacket is reduced. If the lens is contaminated, the absorption coefficient β of the lens will increase rapidly, forming a more serious thermal lens effect. This phenomenon often occurs in actual work. 4 The impact of thermal lens effect on beam quality and laser processing
Impact on beam quality
The thermal lens effect of the ZnSe output mirror causes the output beam to self-focus. As the laser output power continues to increase, the self-focusing phenomenon will become more serious. Due to the deformation of the output mirror, the diameter of the output spot becomes smaller Impact on laser processing (1) Due to the reduction of laser power, the laser power density after focusing will inevitably be reduced, affecting the processing quality. (2) Due to the focusing effect of the output mirror, the far-field beam diameter will become smaller. Because after focusing, the spot size is inversely proportional to the beam diameter before focusing, so as the focused beam diameter increases, the power density will become lower. (3) As the diameter of the beam before focusing becomes smaller, the power density endured by the focusing mirror increases, causing the focusing mirror to produce a thermal lens effect and the focusing focus to shift.
Methods to extend the service life of lasers
At present, steel companies generally use peripheral water cooling to prevent thermal deformation and thermal failure of the output mirror. The control system can control the start and stop of the chiller and complete the use of the laser. When the temperature, flow rate, pressure and other parameters of the cooling water of the chiller meet the set requirements, the laser is allowed to emit light. When an abnormality occurs in the circulating chiller, or when the cooling water parameters exceed the allowable range, the laser should be shut down in time and relevant alarm information should be displayed to help on-site operators troubleshoot in a timely manner. Through laser cutting and welding control systems, laser control and fault diagnosis can be achieved. In addition, cooling measures must be taken on the pipe wall to reduce the temperature of the gas in the pipe, otherwise the output power will continue to decrease until it reaches zero. In order to increase the output power of the laser and extend the service life of the laser, when the external temperature cannot be changed, the gas in the laser must be cooled, and the following points must be ensured:
(1) Regular cleaning of the water cooling device through inspection means, Ensure the water cooling effect of the ZnSe window;
(2) Strictly ensure the purity of the laser working gas, keep the gas clean, and avoid contamination of the inner surface of the output mirror;
(3) Purge the outer surface of the output mirror of the welding machine laser with nitrogen , take away the heat generated by the output mirror when the laser is working; at the same time, it generates positive pressure in the optical path part of the laser output mirror, reducing the occurrence of laser welding machine failure and shutdown, reducing the incidence of laser output mirror failure, and improving production efficiency.
(4) There should be a certain pressure difference between the inside and outside of the optical path to continuously maintain the sealing of the optical path to prevent dust in the air from entering the laser and causing contamination of the outer surface of the lens; in addition, under the same welding power and welding speed, using fiber lasers can achieve better results. Small melt width and small heat affected zone. The melting width of the fiber laser welding sample is about 1/2 of the CO2 laser welding sample. This is because the material has a high absorption rate of the fiber laser laser and easily forms the “keyhole” required for deep penetration welding, and the energy of the laser beam can pass through The keyhole, the metal vapor in the keyhole and the plasma in the keyhole are transmitted to the depth of the material, and the resulting deep penetration welding seam is narrow and deep.