With the development of science and technology, laser technology, as an advanced processing method, has been widely used in the manufacturing industry. As the basic process equipment for industrial production, the manufacturing accuracy and efficiency of molds affect the quality and production cost of products. Traditional mold parts processing methods are difficult to meet the high requirements of modern manufacturing in some aspects, and laser processing technology has gradually become a new favorite in the mold manufacturing field with its high precision, high efficiency and non-contact characteristics. Laser processing technology can not only achieve precision cutting and welding of metal materials, but also perform surface treatment and micro-processing. Therefore, laser processing technology has great potential in improving mold manufacturing processes, improving product quality and productivity.
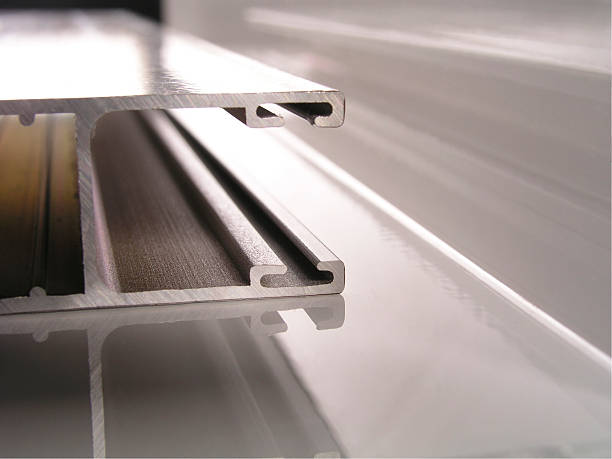
Challenges and Problems of Laser Processing Technology in Mold Manufacturing
Technical Challenges Laser processing technology has many technical challenges in mold manufacturing.
(1) Precision control. Laser processing technology needs to achieve high-precision processing in mold manufacturing to meet the precision requirements of the mold. However, there are some factors in the laser processing process, such as processing heat influence and beam transmission, which will affect the processing accuracy. For the use of laser cutting technology to manufacture automotive molds, due to the problem of beam transmission in the laser processing process, the size of the cut mold parts will deviate from the design requirements. It is necessary to optimize the overall beam transmission system and use higher quality beam transmission devices to solve this problem, but precision control is still an important challenge.
(2) Material adaptability. Laser processing technology needs to adapt to the processing of various materials, including metals, ceramics, plastics, etc. Different materials have different optical and thermal properties, so the laser processing process needs to optimize parameters and control processes for different materials. For the molds of electronic products manufactured using laser welding technology, different materials require different laser powers and welding speeds. In order to solve the problem of material adaptability, it is necessary to conduct experimental research and optimize laser welding parameters to develop different welding processes for different materials. Solving the material adaptability and improving the welding quality and production efficiency of the mold are also important challenges.
(3) Surface quality. During the laser processing process, some surface defects such as ablation and pores may be generated. These defects will affect the service life and processing quality of the mold. Therefore, how to control and reduce surface defects is also an important challenge. For the molds of aircraft engines manufactured using laser drilling technology, ablation and pores are easily generated during the laser drilling process, resulting in the surface quality of the mold parts not meeting the requirements. In order to improve the surface quality, it is necessary to optimize the laser processing parameters and use lower laser power and higher processing speed to reduce the generation of ablation and pores, which puts higher requirements on the processing technology.
Consideration of economic costs and environmental impacts
When considering economic costs and environmental impacts, the following aspects also need to be considered:
① Equipment investment cost. The investment cost of laser processing equipment is high, especially high-power laser equipment, which will increase the initial cost of mold manufacturing;
② Energy consumption. The laser processing process requires a large amount of electrical energy to provide laser energy. The energy consumption of high-power laser equipment is high, which will increase energy costs;
③ Material loss. Laser processing requires the removal of materials during the mold manufacturing process, which will lead to material loss. Although laser processing has less loss than traditional mechanical processing, the cost of materials and resource utilization efficiency still need to be considered;
④ Waste treatment. Laser processing will produce waste, such as cutting or evaporation material residues. These wastes need to be treated, which increases the cost of waste treatment and affects the environment;
⑤ Emission treatment. The laser processing process will produce smoke, exhaust gas and other emissions. Appropriate measures need to be taken to treat and purify them to meet environmental protection requirements, which increases the investment and operating costs of environmental protection. Laser processing technology has great potential in mold manufacturing, but when considering economic costs and environmental impacts, factors such as equipment investment, energy consumption, material loss, waste disposal and emission treatment still need to be considered comprehensively to ensure the sustainable development of laser processing.
Future Outlook and Development Trends
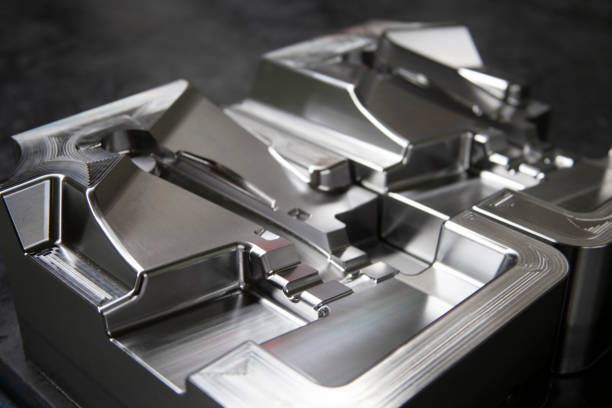
Research and Development Trends of New Laser Technologies
With the continuous development and progress of laser technology, many new laser technologies have emerged.
(1) Ultrafast laser. Ultrafast laser has a short pulse width, measured in nanoseconds, femtoseconds or even sub-femtoseconds. In mold manufacturing, ultrafast laser can be used for precision micro-machining, such as micro-hole machining, micro-cutting and micro-welding. In addition, ultrafast laser can also be used for surface modification, such as nanostructure formation and surface hardening, to improve the wear resistance and corrosion resistance of mold parts.
(2) High-power laser. High-power laser can achieve high energy density processing effect and has a wide range of application potential in mold manufacturing. For example, high-power laser can be used for deep hole drilling, large-size part cutting and welding processes to improve processing efficiency and precision. In addition, high-power laser can also be used for rapid heat treatment and mold part surface modification to enhance the hardness and wear resistance of mold parts.
(3) Fiber laser. Fiber laser has the characteristics of small size, high beam quality and good stability, and is widely used in mold manufacturing. Fiber laser can be used for cutting, welding and marking of mold parts, and can also flexibly process complex shapes and difficult-to-process parts. The application of fiber laser can also realize remote processing and automated production, improving production efficiency and quality. The research and development and application of the above-mentioned new laser technology will further promote the development of the mold manufacturing industry. By improving processing accuracy, reducing production costs and improving production efficiency, the new laser technology will bring more opportunities and competitive advantages to mold manufacturing companies.
Application prospects of intelligence and automation in laser processing
Intelligence and automation are the current trends in industrial manufacturing, and are also of great significance to the development of laser processing technology. In the future, intelligence and automation will play an increasingly important role in laser processing and have broad application prospects. In terms of intelligence, with the continuous development of technologies such as artificial intelligence and machine learning, data collection, analysis and processing in the laser processing process will become more refined and automated. By analyzing real-time monitoring data and historical data, the efficiency and quality of laser processing can be improved, and costs and risks can be reduced. For example, machine learning algorithms can be used to optimize and automatically adjust laser processing parameters, thereby improving processing efficiency and accuracy. In terms of automation, laser processing equipment will become increasingly intelligent and automated. By introducing automation systems, robots, sensors and other devices, the automated control and intelligent management of the laser processing process can be achieved, which can not only improve the stability and consistency of the laser processing process, reduce errors and deviations caused by human intervention, but also achieve automated control and management of the entire process, further improving production efficiency and quality. In the future, with the continuous development and application of technologies such as artificial intelligence, machine learning, and the Internet of Things, intelligence and automation will bring more opportunities and challenges to laser processing, and promote the development of laser processing technology.
The embodiment of green manufacturing and sustainable development concepts in laser processing
Laser processing has been highly sought after in recent years and has replaced traditional processing techniques in some fields. Cleanliness and environmental protection are key factors. Laser cleaning makes the mold processing process more environmentally friendly. It uses high-energy laser beams to interact with the substances to be removed on the surface of the workpiece, allowing the attached substances to evaporate or peel off instantly to achieve the purpose of cleaning the workpiece. This processing technology does not require chemical cleaning agents and is green and pollution-free. The popularization of laser cutting technology has, to a certain extent, made up for the shortcomings of high pollution and high consumables of traditional processing techniques (plasma cutting, flame cutting, etc.). At the same time, with the breakthrough of high-power, high-brightness laser technology and the continuous advancement of cutting technology, the dust generated by laser cutting will also be reduced. In general, the embodiment of green manufacturing and sustainable development concepts in laser processing is as follows.
(1) Energy saving and emission reduction. Laser processing is more energy-saving and efficient than traditional mechanical processing methods. During laser processing, the laser beam acts directly on the material, without the need for a large amount of energy to push mechanical parts such as tools, thus reducing energy consumption. In addition, laser processing can also achieve precise control and small-size processing, reducing material waste and reducing the cost of waste generation and disposal.
(2) Waste-free production. Laser processing is a non-contact processing method that does not require contact with the workpiece and does not cause physical damage or wear to the workpiece. Compared with traditional processing methods, laser processing does not have the problem of waste generation and debris, thus achieving waste-free production.
(3) Fine processing and optimized design. Laser processing has the characteristics of high precision and high flexibility, and can realize the processing of complex shapes and small sizes. In the process of product design and manufacturing, more attention can be paid to optimized design, reducing the use and waste of materials, and realizing the effective use of resources.
Conclusion
The application of laser processing technology in the field of mold manufacturing has made rapid progress, bringing opportunities and challenges to the mold manufacturing industry. The continuous development and innovation of new laser technologies have provided more efficient, more precise and more flexible solutions for mold manufacturing. From ultrafast lasers to high-power lasers, and then to fiber lasers, these new technologies continue to promote the progress of mold manufacturing. Through laser processing technology, mold manufacturing companies can achieve higher production efficiency and better quality, while reducing costs and human resources. Laser processing technology can be applied to micro-processing, cutting, welding and other processes of mold parts to improve processing accuracy and processing speed. Laser processing can also realize the processing of complex shapes and difficult-to-process parts, bringing better flexibility and innovation to mold manufacturing. Laser processing technology still needs to solve a series of technical problems in mold manufacturing. Future research and development should focus on solutions to these problems and the development and application of innovative technologies. Through continuous research and improvement, the application of laser processing technology in mold manufacturing will be more extensive. With the continuous innovation of laser technology, laser processing technology will bring more opportunities and competitive advantages to the mold manufacturing industry and promote the industry to a higher level.