In order to improve the consistency and yield rate of products after laser cutting, it is necessary to accurately position the plates that are loaded during cutting. However, because wooden boards have a certain degree of elasticity and have large dimensional errors and are easily deformed, and the boards are stacked at random positions in the loading bin, pre-positioning is required before processing and clamping to ensure the positioning accuracy of the right-angle origin of the square boards ( (Reduce the error between workpiece coordinates and processing coordinates) and then use the robot suction cup to grab and transport it to the laser cutting machine processing area. After the loading manipulator places the plate on the laser cutting machine, the position of the plate will also be offset due to warping deformation. Therefore, after completing the positioning and grabbing, the laser cutting machine should also fix and support the processed plate to ensure the processing process. Done successfully. Laser cutting equipment mainly uses dual-station processing. After completing the automation upgrade, the goal is to achieve 24-hour unmanned production and increase production capacity. The overall laser cutting flexible production line processing rhythm is not slower than 30 s/group.
System hardware design
According to the project needs and goals, the overall system structure design is divided into four parts: loading pre-positioning unit, industrial robot handling unit [4], laser cutting tooling, and unloading transfer unit.
Loading pre-positioning unit
This laser cutting flexible production line system completes laser cutting in a dual-station processing method of 2 pieces per group. Therefore, in order to ensure the positioning accuracy of the industrial robot handling unit, the processing plate needs to be processed before the industrial robot grabs it. Make pre-positioning. According to the two pre-positioning processes, the loading pre-positioning unit is mainly divided into two areas. In the stacking and sorting area, the pile of board materials is first stacked and sorted, and the pile of board materials is limited to a local space through the horizontal adjustment of the fence. The three-axis manipulator completes the suction cup grabbing and movement to accurately locate the area to be grabbed. The area to be grabbed is accurately positioned and moved horizontally through the limit mechanisms in the X-axis and Y-axis directions, so that the plate has a relatively consistent workpiece coordinate origin when it is grabbed by the six-axis industrial robot.
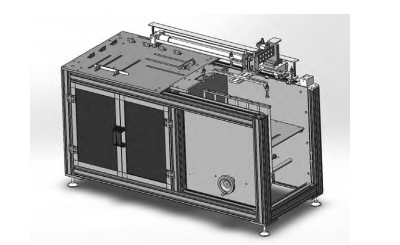
Industrial robot handling unit
The industrial robot handling unit mainly includes two parts: the six-axis industrial robot body and the suction cup clamp (see Figure 3). The six-axis industrial robot handling control signal is provided by the PLC end. The control signals of the solenoid valve corresponding to the suction and grasping are also uniformly output by the PLC. The suction cup adopts a symmetrical structure and contains 8 pneumatic circuits, which can evenly absorb all positions of the plate and smoothly grasp the positioned processed plate. When the laser cutting product model changes Finally, the position of the suction cup can be adjusted according to changes in product size.
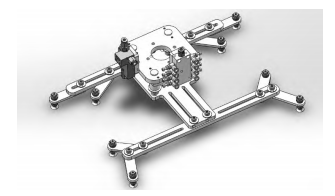
Laser cutting tooling
Wooden boards have a certain degree of elasticity and the thickness of the processed boards is thin and easy to deform. After the loading manipulator places and positions the processed boards on the laser cutting machine tooling, if the processed boards lack adequate fixation and support, the board will The position will also shift due to warpage deformation, ultimately affecting the machining accuracy. The laser cutting double-station tooling secures the edge of the plate with press-buttons (see Figure 4), and multi-point pillars are used in the middle area to support the processed plate. Considering that the shape of laser cutting is not fixed, the multi-point pillars responsible for support can also be used Flexibly adjust the support position through the mechanical structure to avoid the laser cutting area. The laser cutting tool uses a tablet pressing cylinder to drive the corresponding press buckle fixing mechanism. When the cylinder extends, the locking mechanism presses down to complete the fixation of the processed plate; taking into account the subsequent blanking and grabbing action, when the tablet pressing cylinder retracts , the locking mechanism should rise and open and must be released to the outside of the processing area, so a trigger structure is specially designed in the press button fixing structure. When the tablet pressing cylinder retracts, the trigger structure will be stressed to generate a moment of flipping outward. Ensure the flip direction of the press buckle released after processing is completed.
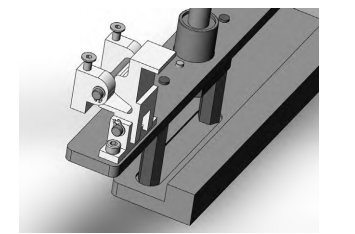
Schlussfolgerung
The article designed a flexible production line loading and unloading system suitable for laser cutting equipment, which realizes the automation and unmanned production of the plate laser cutting process, improves the positioning accuracy of product processing and the consistency of finished products, and reduces the scrap rate. Enterprises The effect of cost reduction and efficiency improvement is obvious. The design system only verified the feasibility of the project application. The details of the laser cutting process and the performance of industrial robot grabbing still need to be further explored, especially on the premise of ensuring the positioning accuracy of multi-station laser cutting. The efficiency of clamping, loading and unloading, maximizing production line capacity and ensuring product quality are the main research directions and optimization goals in the future.