Laser cutting principle
Laser is the product of stimulated radiation. Its production is inseparable from three key elements: working material, pump and resonant cavity. After absorbing energy, low-energy level particles will transition to high-energy level orbits, but the state of high-energy level particles is unstable and will Falling to a low-energy orbit and emitting photons at any time, laser light is generated when many particles emit photons with high consistency at the same time. Laser processing can be divided into hot processing and cold processing according to the size of photon energy. Cold processing is generally used in the laser marking process of plastic parts. The laser completes the separation of molecules and substances by destroying the molecular bonds of the material. During this process, the material will not cause thermal damage, thermal deformation and other problems. Thermal processing is more widely used, such as laser cladding, laser welding, laser cutting, etc. During the laser cutting process, the laser beam forms a small focus on the surface of the material under the action of the focusing mirror, and the material around the focus absorbs the laser. The energy is quickly heated to melting, and the molten metal separates from the material under the blowing of the auxiliary gas to form a slit, thereby completing the entire cutting process.
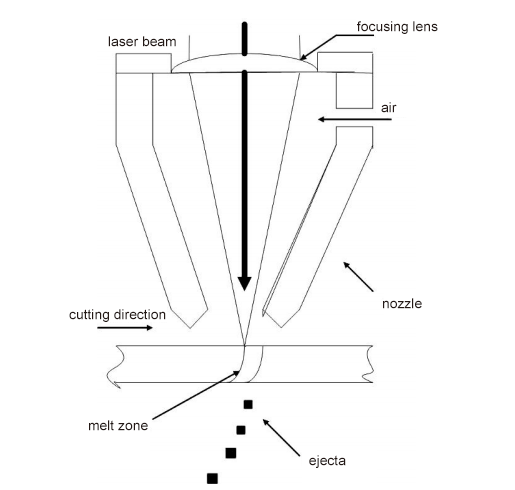
According to the different physical manifestations of cutting materials, laser cutting can be roughly divided into: laser melting cutting, laser vapor cutting, laser reaction melting cutting and laser controlled fracture cutting.
(1) Laser melting cutting refers to the fact that during the laser cutting process, the focused laser beam causes evaporation inside the material to form holes. The resulting hole appears as a black body, which causes the laser absorption rate to increase rapidly, and the metal wall of the small hole is melted. Surrounded, enlarged and deepened, and then blown out by the action of high-pressure coaxial gas.
(2) Laser vaporization cutting means that the material to be cut is heated to vaporize in a very short time, and the vaporized material is blown away from the cutting surface under the action of the auxiliary gas flow. Gas cutting can only be used for materials that are difficult to melt, such as wood, carbon and certain plastic materials. Materials processed in this way can often achieve very high cutting quality.
(3) Laser reaction melting cutting, also called laser oxygen-assisted cutting, is a special melting cutting method that uses oxygen as the auxiliary gas. During the cutting process, the high-energy laser beam heats the material to the ignition point temperature. At this time, the material has not yet melted. However, when the material reaches the ignition point, oxygen will react violently with the material, releasing a large amount of oxidation reaction heat, and then the material will begin to melt. The melting forms a metal molten substance accompanied by the formation of a large amount of oxides. The molten substance is blown away from the surface of the cutting seam by the auxiliary gas flow, and the cutting process is completed. In the laser oxygen cutting process, the main reason for using oxygen as an auxiliary gas is that oxygen is one of the important substances involved in the oxidation and combustion reaction of the material. The combustion reaction will not occur when using other types of auxiliary gases. To complete the cutting, the laser beam is required to provide more energy is required to ensure that the metal changes to a molten state. In the laser oxygen cutting process, the additional energy provided by the combustion reaction can reach 70% of the total cutting energy. In the reactive melting cutting of titanium alloy, it provides nearly 90% of the energy. The iron-oxygen combustion reaction will generate many oxidized melts. These melts generally have low viscosity and are easy to be removed under the action of auxiliary gas. Most of them are ferrous oxide, and there are also a small amount of iron oxide and ferric oxide . Due to the low viscosity of the melt, it is easier to be blown away from the bottom of the material by the auxiliary gas, reducing the possibility of slag adhering to the bottom of the cutting. At the same time, the oxides generated by the combustion reaction increase the laser absorption rate, which is beneficial to absorbing more laser energy.
(4) In laser controlled fracture cutting, cracks are caused by the material absorbing laser energy and heating up. The stress near the laser focus changes due to high temperature. When the laser beam passes through, these compressive stresses relax and form local residual tensile stresses. Under the action of stress, the cracks will continue to extend in the direction of laser movement, and the material will fracture and separate along the path of the laser beam. This cutting method is particularly suitable for cutting brittle materials such as ceramics .
Influencing factors and evaluation criteria of laser cutting
Influencing factors of laser cutting
The laser cutting process contains complex physical relationships, involving the interaction between the material to be cut, the laser and the auxiliary gas. There is energy in this process. Changes in temperature field, thermochemical reactions, flow dynamics and aerodynamics. J Fieret has studied the influencing factors of laser cutting and summarized a variety of influencing factors, which can be roughly divided into three categories: the first category includes some inherent characteristics of the material, and the second category is mainly the related parameters of the laser and laser equipment. . The third category is process parameters closely related to the laser processing process. Generally speaking, when conducting research on laser cutting, the relevant properties and parameters of materials and equipment are determined and difficult to change. Therefore, in order to improve cutting quality and increase cutting efficiency, we can only work on the processing process parameters. Therefore, this paper selects laser power, cutting speed, laser frequency, laser duty cycle and auxiliary gas pressure as input parameters to study their impact on cutting quality characteristics.
(1) Laser power: Laser power is the energy power input to the laser. The intensity of the laser beam can be calculated by dividing the power by the laser spot area. The size of the laser power directly determines the cutting ability and cutting efficiency. However, the bigger the laser power, the better. Too much laser power will lead to an increase in the kerf width and heat-affected zone, and even over-burning of the workpiece, which is serious. Impair processing quality.
(2) Cutting speed: In laser cutting, the cutting speed is directly related to the processing efficiency. The greater the cutting speed, the higher the processing efficiency. However, the cutting speed is restricted by the processing quality. Excessive cutting speed will lead to the inability to cut through the material. , causing the workpiece to be scrapped, but too small a cutting speed will affect the processing efficiency and cause a decrease in factory profitability. Therefore, it is very important to determine the cutting speed when performing laser cutting.
(3) Gas pressure: The main function of the auxiliary gas is to remove the molten metal at the cutting seam to ensure the smooth progress of laser cutting. Generally speaking, the greater the gas pressure, the stronger the removal ability of molten material. However, if the gas pressure is too high, the air flow speed at the nozzle will increase, and the air flow will be disturbed at the slit, which will reduce the ability of the gas to remove molten material and increase the cooling capacity. , thus greatly increasing the probability of slag hanging at the slit. Using nitrogen as an auxiliary gas to cut stainless steel can obtain non-oxidizing, bright cutting edges. For low carbon steel, oxygen can be used as an auxiliary gas to improve cutting efficiency and use lower laser power to complete cutting.
(4) Laser frequency: When the average laser power is constant, the higher the laser frequency, the more laser pulses the laser emits per unit time, and the lower the energy carried by a single laser pulse. When cutting, it is like using a Use a dull knife to cut the material.
(5) Laser duty cycle: The laser duty cycle will affect the peak power of the laser. For example, when the laser duty cycle is 10%, the peak power of the laser can reach 10 times the average power. When the average laser power is constant, the laser The larger the duty cycle, the smaller the laser peak power. When the laser duty cycle is 100%, the average laser power is equal to the peak power. The cutting test material in this paper is Q235 low carbon steel, and the relevant physical properties cannot be changed. The laser beam characteristics are mostly determined by the laser, and the parameters of the laser have been determined from the factory. Therefore, the main processing parameters that need to be considered and changed in actual processing are the processing parameters. According to the operability and actual situation of the laser cutting equipment, this article mainly changes the laser power, cutting speed, laser frequency, laser duty cycle and auxiliary gas pressure. parameters to test.
Determination criteria of laser cutting quality
In the process of laser cutting, if the process parameters are improperly selected, it will affect the processing efficiency and increase the operating cost of the factory, or produce various processing defects as shown in picture.
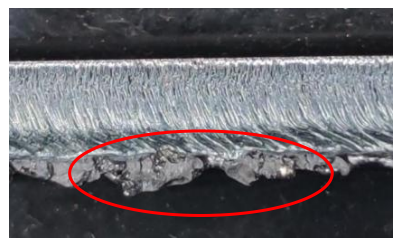
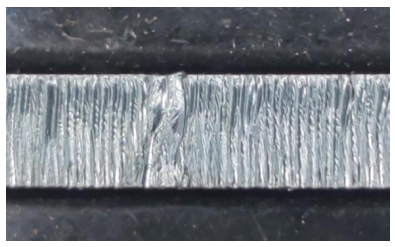
The evaluation standards for cutting quality were first obtained by foreign researchers by referring to relevant German standards . Commonly used criteria for evaluating cutting quality in daily laser cutting processing are: cutting width, incision surface roughness, slag adhesion at the bottom of the slit, heat-affected zone width and cutting stripes .
(1) Cutting width. The kerf width refers to the shortest distance between both sides of the kerf, and is usually related to the laser mode and laser spot size. Generally speaking, the larger the kerf width, the worse the cutting quality.
(2) Cut surface roughness. There are many evaluation methods for surface roughness, such as the average arithmetic deviation of the curve (average roughness) Ra, the average height of unevenness Rz and the maximum height Ry. The first two are commonly used to evaluate roughness. For the laser cutting incision section, the average roughness Ra can be used for evaluation. Since the laser cutting incision roughness value has a layered distribution phenomenon in the thickness direction, the closer to the lower surface the rougher the worse it is. Therefore, the distance below is usually selected. Measure at 1/3 of the surface.
(3) The amount of slag attached at the bottom. During the laser cutting process, the molten metal material moves toward the bottom of the slit under the action of gravity and auxiliary gas. Some viscous molten materials have not had time to be blown away from the slit surface by the auxiliary gas during the movement. It is re-solidified under the cooling effect of the air flow, thus forming hanging slag. Therefore, the viscosity of the melt is reduced, its fluidity is improved during the movement of the slit, and the generation of dross can be reduced. The generation of slag during laser cutting operations needs to be avoided. In some cases, when it is impossible to obtain slag-free cutting parts by changing the cutting process, a grinding process is often added to remove the slag. Therefore, the less or even no slag hanging amount can improve the quality of cutting parts, reduce subsequent processing steps, and save costs.
(4) Width of heat affected zone. During the material cutting process, heat diffuses from the slit to the surrounding area. The material in the area around the slit undergoes phase changes or changes in grain size. The strength and hardness of the material in these areas undergo subtle changes, which are called heat-affected zones. The width of the heat affected zone is one of the relevant indicators that reflects the cutting quality.
(5) Cutting stripes. Cutting stripes are one of the characteristics used to evaluate cutting quality. The generation of laser cutting stripes is almost inevitable. The difference is that some are obvious and some are almost invisible to the naked eye. Everyone has different opinions about the cause of the cutting stripes, and researchers have not obtained a consistent answer. Generally speaking, the smaller the cutting stripes and the shallower the depth, the better the cutting quality.