In the ever-evolving landscape of metal fabrication, innovative companies are constantly seeking new ways to enhance their capabilities and stay ahead of the competition. One such advancement that is revolutionizing the industry is laser-cut tube technology. This cutting-edge approach is transforming how metal fabricators operate, offering unprecedented precision, efficiency, and versatility in tube cutting processes.
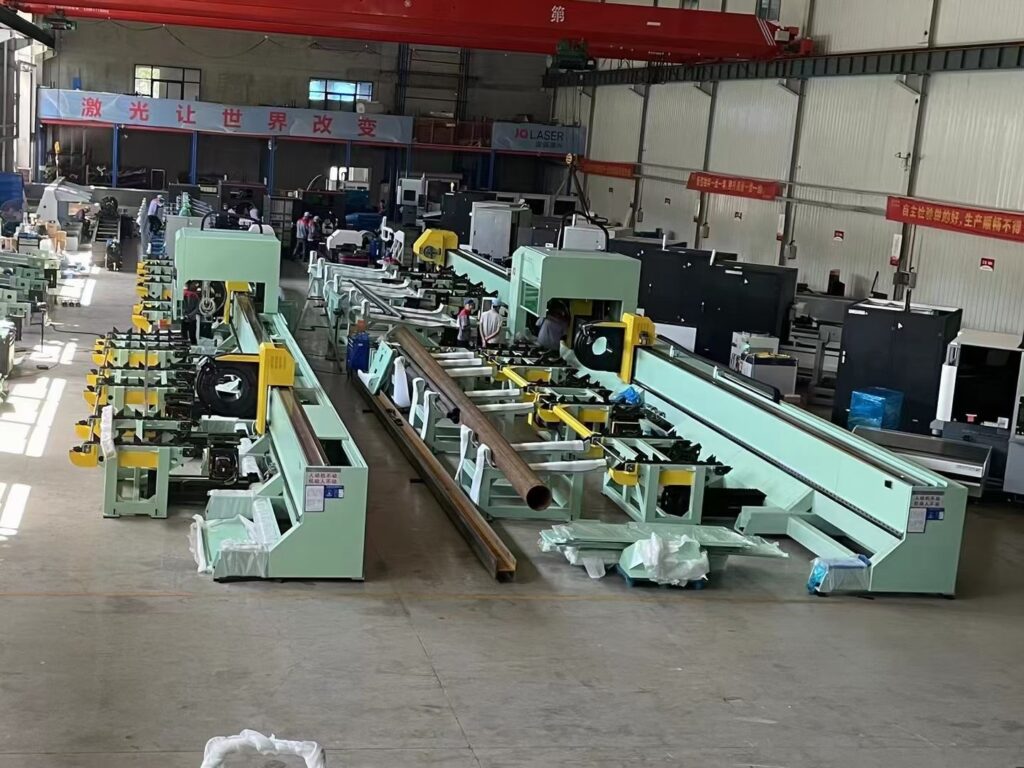
Laser-Cut Tube Technology Overview | |
---|---|
Wichtigste Vorteile | Precision, Efficiency, Versatility |
Industries Impacted | Automotive, Aerospace, Construction, Healthcare |
Machine Capabilities | Multi-axis cutting, Complex geometries, Automation |
Material Range | Steel, Aluminum, Copper, Titanium |
Typical Applications | Structural components, Exhaust systems, Medical devices |
Overview of Laser-Cut Tube Technology
In the ever-evolving landscape of metal fabrication, innovative companies are constantly seeking new ways to enhance their capabilities and stay ahead of the competition. One such advancement that is revolutionizing the industry is laser-cut tube technology. This cutting-edge approach is transforming how metal fabricators operate, offering unprecedented precision, efficiency, and versatility in tube cutting processes.
Key Benefits of Laser-Cut Tube Technology
Laser-cut tube technology represents a significant shift in metal fabrication approaches. This advanced system offers numerous benefits over traditional cutting methods, including increased precision, reduced processing times, and enhanced versatility in material handling.
Elimination of Post-Processing Needs
One of the key advantages of laser-cut tube technology is its ability to eliminate the need for extensive post-processing. By using nitrogen as an assist gas, the laser can produce clean cuts that require minimal deburring or descaling before welding. This streamlined process not only saves time but also improves the overall quality of the finished products.
Complex Designs and Customization
The capabilities of laser-cut tube technology extend beyond simple cutting operations. It allows metal fabricators to create complex designs and intricate patterns that were previously difficult or impossible to achieve with conventional methods. This opens up new possibilities for product innovation and customization, enabling companies to meet the evolving demands of their diverse customer base.
Strategic Growth for Metal Fabricators
Metal fabricators investing in laser-cut tube technology are not just improving current operations; they’re making a strategic move to position themselves for future growth. By expanding their capabilities, these companies are looking to tap into new markets and industries that require high-precision tubular components.
Industry-Wide Impact of Technological Advancements
The impact of this technological advancement extends beyond individual companies. As metal fabricators explore new applications for laser-cut tubes, they are contributing to the broader evolution of the metal fabrication industry. The precision and efficiency offered by laser cutting are setting new standards for quality and productivity across various sectors, from automotive and aerospace to furniture and material handling.
Challenges of Embracing New Technology
Industry leaders recognize that embracing this technology is not without its challenges. The investment in new equipment and the need for skilled operators to run the complex machinery represent significant commitments. However, forward-thinking companies view these as necessary steps to stay at the forefront of the industry and meet the increasing demands for high-quality, precision-engineered components.
Aligning with Industry 4.0 Trends
The adoption of laser-cut tube technology aligns with broader trends in manufacturing towards greater automation and digitalization. As Industry 4.0 concepts continue to reshape the manufacturing landscape, metal fabricators are positioning themselves to integrate these advanced systems with emerging technologies such as IoT (Internet of Things) and AI (Artificial Intelligence) to further optimize their production processes.
Future Growth Strategy with Laser Technology
Looking ahead, metal fabricators see laser-cut tube technology as a cornerstone of their future growth strategy. Many are actively exploring new applications and markets where their enhanced capabilities can provide value. From lightweight structural components for the aerospace industry to complex tubing systems for medical devices, the possibilities are vast and exciting.
Workforce Development and Training
The commitment to innovation in the metal fabrication industry is not limited to equipment investments. Companies are also focusing on developing the skills of their workforce to fully leverage the potential of the new technology. Training programs and partnerships with educational institutions are being established to ensure a pipeline of skilled operators and technicians who can drive technological vision forward.
Speed and Productivity Advantages
Laser tube cutting machines offer significant speed and productivity advantages over traditional cutting methods. The combination of high-power laser sources, fast axis movements, and intelligent control systems enables manufacturers to achieve unprecedented throughput rates.
High Cutting Speeds and Rapid Piercing
High cutting speeds are a key benefit, with fiber laser powers reaching up to 8 kW or more, allowing tube laser cutting machines to achieve cutting speeds several times faster than traditional methods. This high-speed cutting capability dramatically reduces cycle times, allowing manufacturers to process more parts in less time.
Automated Material Handling Systems
Automated material handling systems further enhance productivity. Tube laser cutting machines can be equipped with automated loading and unloading systems, eliminating manual handling of tubes, reducing setup times, and enabling continuous, unattended operation. By minimizing operator intervention, manufacturers can maximize machine utilization and boost overall output.
Long-Term Cost-Effectiveness
Investing in laser-cut tube technology offers long-term cost-effectiveness and a strong return on investment for metal fabricators. While the initial capital expenditure may be higher compared to traditional cutting equipment, the benefits quickly justify the investment.
Reduced Labor and Material Costs
Reduced labor costs are a significant factor. The high level of automation and the elimination of secondary processes, such as deburring and finishing, significantly reduce labor requirements. Skilled operators can focus on high-value tasks, while the machine handles the cutting process autonomously, optimizing labor utilization and lowering overall labor costs.
Increased Throughput and Efficiency
Increased throughput is another key benefit. The high cutting speeds and productivity of tube laser cutting machines enable manufacturers to process more parts in a given time frame. This increased throughput allows for faster order fulfillment, shorter lead times, and the ability to take on more projects, ultimately leading to revenue growth and improved customer satisfaction.
Maintenance and Tooling Cost Reduction
Maintenance and tooling costs are also reduced. Traditional cutting methods often require frequent tool changes, sharpening, and maintenance, which can be costly and time-consuming. In contrast, tube laser cutting machines have lower maintenance requirements and eliminate the need for physical cutting tools. The laser source itself has a long lifespan, and the machine’s robust design ensures reliable operation with minimal downtime.
Leading the Future of Metal Fabrication
As metal fabricators continue to push the boundaries of what’s possible with laser-cut tube technology, they are setting an example for others looking to future-proof their operations. The industry’s journey demonstrates that embracing cutting-edge technology is not just about staying competitive; it’s about reimagining the possibilities of metal fabrication and creating new opportunities for growth and innovation.
Conclusion: The Future of Metal Fabrication
The adoption of laser-cut tube technology represents a bold step into the future of metal fabrication. By leveraging the precision, efficiency, and versatility of this advanced system, companies are not only enhancing their current capabilities but also paving the way for new advancements in the industry. As metal fabricators continue to explore the full potential of laser-cut tubes, they are poised to play a significant role in shaping the future of metal fabrication, one precision cut at a time.