The main part of the hydraulic support is composed of structural parts of medium-thick steel plates and oil cylinders. As shown in Figure 1, the structural parts composed of medium-thick steel plates account for about 79% of the total weight of the hydraulic support. The raw materials are mainly medium-thick steel plates with a thickness of 16 mm ~ 50 mm. For the cutting of medium-thick steel plates, the traditional cutting equipment is mainly flame cutting machines and plasma cutting machines. To a certain extent, plasma and flame cutting equipment are prone to uneven shrinkage and a certain degree of thermal deformation when cutting and blanking, and kerf compensation is prone to occur during cutting and shaping, which cannot effectively guarantee cutting accuracy. Poor cutting quality will lead to problems such as difficulty in assembling and positioning structural parts, excessive machining allowances, etc. In severe cases, it may even cause hydraulic supports to cause serious safety hazards to underground production and the safety of coal miners during coal mining. In order to ensure that the hydraulic support structural parts meet the tolerance dimensions of drawings and processes when cutting and blanking, there are a large number of machining processes in the hydraulic support structural parts process plan, which greatly affects the production and processing rhythm of structural parts.
1 Application of laser cutting
(1) Application principle of laser cutting
At present, the research on the working principle and process method of laser cutting thin plates has been quite in-depth, but there are relatively few research reports on the laser cutting process of thick plates. For laser cutting of medium and thick plates, it is necessary to add active gases such as oxygen as auxiliary gas in the laser beam, and use high-density energy to converge into a small space to heat the workpiece through the laser beam, causing the temperature of the metal or non-metal workpiece to rise rapidly. The melting and boiling points of the material are reached in a very short period of time, causing the material to begin to melt rapidly and vaporize to form steam. And rely on the dynamic effect of auxiliary gas to blow the molten slag out of the incision, thereby forming an incision on the material.
(2) Characteristics of laser cutting
Compared with traditional flame cutting and plasma cutting methods, the most important professional advantage of laser cutting in metal material cutting is faster production and cutting processing speed and higher cutting quality. As shown in Figure 2, after laser cutting of metal materials, the width of the heat-affected zone at the cutting position is very small, the performance of the material near the cutting seam is almost unaffected, and the workpiece deformation is small. The cutting surface is not prone to slag and oxide scale. Some hydraulic support structural parts can even be used as the last processing step after blanking and cutting. There is no need for mechanical processing, and the parts can be directly used for welding and assembly.
Laser cutting is a type of thermal cutting. During the cutting process, about 0.1 ~ 0.3 mm of material is removed. Secondly, thermal processing will produce thermal deformation. See Table 1 to illustrate the relationship between material thickness, part size and error.

(3) Factors affecting laser cutting plate thickness
During laser cutting, the power of the laser generator is directly proportional to the fiber laser cutting speed of metal materials, and the choice of laser power also has an essential impact on the cutting plate thickness. The cutting power needs to be determined according to the material of the cutting plate and the thickness of the plate. If the power is too high or too small, a good cutting surface will not be obtained. When laser cutting, the power is too low, which will produce cutting melt stains, and obvious scars will be produced on the cutting section. The selection of appropriate laser power, combined with appropriate cutting gas and gas pressure, can ensure good cutting quality of the product. Therefore, cutting of medium and thick plates requires matching high-power laser cutting equipment to effectively ensure production and cutting accuracy.
2 The impact of laser cutting on traditional processing technology
In order to improve cutting production efficiency and ensure cutting production quality, high-power laser cutting machines and fiber laser cutting machines have become more widely used. As shown in Figure 4, the middle ribs, insert plates, valve plates and other parts of the hydraulic support parts that have been laser cut (without manual grinding and cleaning) have smooth cutting surfaces, no obvious cutting slag, spatter, and oxide scale, and the inner holes It is uniform and smooth, with no obvious cutting defects at the starting point. The measured cutting and blanking error is within ±0.55, which meets the requirements of the drawings and process specifications. Therefore, on the premise of ensuring the cutting quality of the workpiece, the use of laser cutting equipment can appropriately reduce unnecessary processing steps in traditional processes. optimize the process flow, and improve processing efficiency.
(1) After laser cutting, the oxide scale removal in the slag cleaning process can be canceled according to the cutting conditions of the cutting surface, thereby improving the overall production cycle.
(2) For non-slender parts (aspect ratio ≤ 5), after cutting with a 20 kW or 30 kW high-power fiber laser cutting machine, the leveling process can be canceled if the flatness meets the drawing process requirements. If there is no bending For processes such as cutting, beveling, and mechanical processing, the materials can be directly transferred to the supporting process for matching after laser cutting.
(3) When using a high-power laser cutting machine to cut parts with a plate thickness of 10 mm ~ 40 mm, the milling process of the ear plate, balance ear plate, column socket lower rib plate, and positioning rib plate can be appropriately cancelled. The traditional process flow: CNC cutting – cleaning (removing slag and scale) – mechanical processing process is optimized to: laser cutting – cleaning (removing slag), which optimizes the operation process and improves production efficiency.
(4) The unstressed ear plates, valve plates, and cover plate locking pin holes that are not connected to the jack are directly cut by laser blanking, which can eliminate the drilling and boring processes, reduce processing costs, and improve overall production. efficiency.
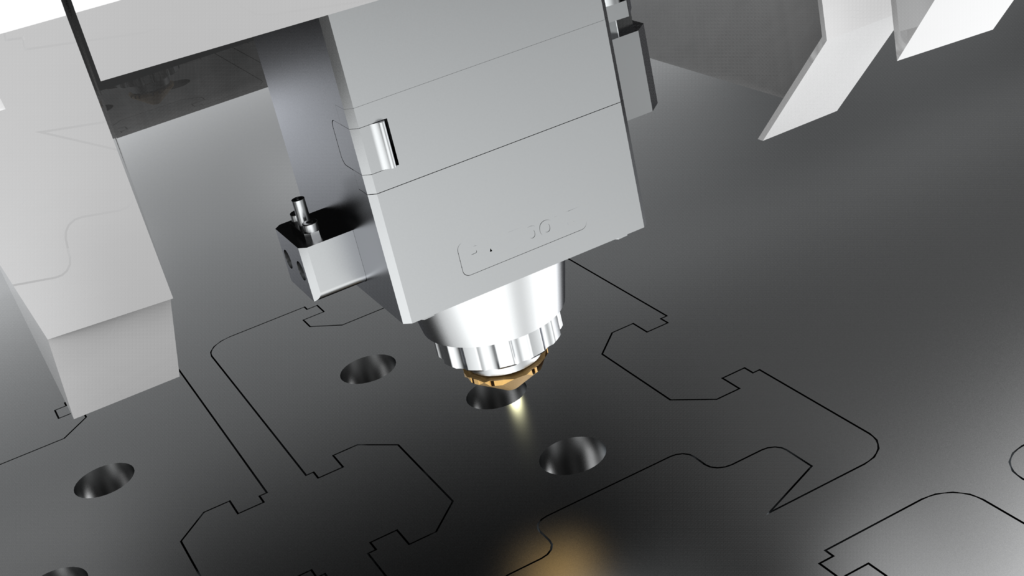
(5) The processing of the hinge holes of the top beam, cover beam, and base can be carried out by the traditional process of pre-cutting holes for the main rib parts – pre-boring the main rib components – and overall boring of the components. Based on the high power of 20 kW and 30 kW The processing process of hinge holes cut by laser cutting machines with plate thicknesses of 10 mm ~ 40 mm is optimized as follows: the main rib parts are pre-cut and then directly transferred to the components. Overall boring, on the basis of ensuring the overall boring allowance, eliminates the pre-boring process of the main rib assembly, which can effectively shorten the logistics transfer cycle.
3 Development of Laser Cutting
At present, laser cutting is developing in the direction of intelligence and production lines. Network interconnection and interoperability are realized through all logistics equipment, laser cutting equipment, and safety and environmental equipment in the production workshop, and then through the cutting equipment and MES production Control, WMS warehouse management, WCS logistics execution system, QMS quality management system are integrated. Ultimately, intelligent functions such as automatic loading and unloading of steel plates for laser cutting equipment, automatic distribution of offline cutting programs, intelligent distribution of cutting tasks, and automatic cutting of parts are realized. It breaks the human-computer interaction production situation in the traditional cutting industry and relies on digital system integration to realize equipment automation, logistics automation and information automation of laser cutting. On the premise of ensuring quality, the cutting production efficiency and overall production capacity of hydraulic support structural parts have been greatly improved.