What Are Laser Cutting Machines?
Laser cutting machines are tools used in various industries for precision cutting and designing projects. They emit a high-powered laser beam to either cleanly cut or etch a specific design on materials such as steel, plastic, or wood. The beam can either burn, vaporize, or melt away the excess product, leaving a superior finished design or edge. These machines are often used in engineering for the precision cutting of components of machines and in industrial applications for cutting structural and piping materials and flat sheet material such as metal. They have settings known as computer numerical control (CNC), which control and direct the laser beam’s intensity for the desired design effect or specific cuts required in a manufacturing or design project. The laser beam is generated by a process where electrical discharges or a lamp trigger a lasing material within a confined container, causing a chemical reaction, resulting in a high-powered beam being released. The beam is then reflected using a mirror in a stream of monochromatic light, and from the mirror, the light is directed by fibre optics or mirrors to the work area, with the narrowest point of the beam cutting or making the design etch on the material1.
How does the laser cutting machine work?
Basic concepts of laser cutting:
Laser cutting utilizes the focused energy of a high-powered laser beam to cut through materials. The process involves directing the laser beam onto the surface of the material, causing localized heating and vaporization or melting. This results in a precise and clean cut along the programmed path. Laser cutting is characterized by its ability to produce intricate designs with high accuracy and minimal material waste. It is widely used across industries for cutting various materials such as metal, wood, plastic, fabric, and more.
Main components of laser cutting machine:
Main components of the product
The main components of the FLT-7028HTS series laser pipe cutting machine include: machine tool host, chain-type automatic loading rack, chain-type automatic unloading rack, control system, low-voltage electrical system, laser, chiller, exhaust fan, etc.
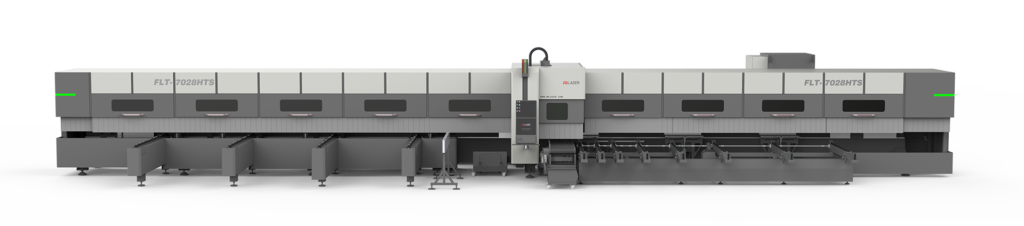
Product detail: New Product JQ Vertical Three Chucks Series
Machine tool host part
The main part of the machine tool is the main component of the entire laser pipe cutting machine. The cutting function and cutting accuracy of the laser pipe cutting machine are realized by the main part. The main part consists of the bed, loading and unloading follow-up support, chuck, X/Z It is composed of shaft device, auxiliary system (protective cover, air path and water path), operation panel and other parts.

Each of the loading and unloading sides is designed with 3 sets of chain loading and unloading devices;
Electrical control part
The electrical control system of the laser pipe cutting machine is an important part to ensure the running trajectories of various graphics. The general electrical control system mainly consists of a numerical control system and a low-voltage electrical system.
This machine tool CNC system is equipped with Baichu’s high-performance bus-based 5000A CNC system. This system is based on the Windows operating platform, runs stably and reliably, and contains a 64-bit microprocessor, which can be used with nesting software.
Low voltage electrical system
The low-voltage electrical system is located in the electrical control cabinet and is the interface part of the electrical control of the entire machine. Various original components of the electrical system are produced by well-known domestic and foreign manufacturers to ensure that the entire machine is stable, reliable and responsive during operation. The drive motor is an AC servo motor. The AC servo motor is used to drive the X-axis, Y-axis, and AW (synchronous rotation) axis of the machine tool. It is characterized by good acceleration performance and fast response speed. The Z-axis of the machine tool is the feed axis and uses AC servo. The motor (with brake) is used to drive: Z-axis cutting head, which is characterized by good dynamic response characteristics and can be controlled by both follow-up and NC.
Compared with traditional lasers, the fiber laser used has higher photoelectric conversion efficiency, lower power consumption and better beam quality. The laser is compact, maintenance-free and ready for use. Due to its flexible laser output mode, it can be easily integrated with system equipment.
Auxiliary peripherals
Including chillers, exhaust systems, etc.
Types of Laser Cutting Processes
1. Fiber Laser (Straight): Fiber laser cutting is a highly efficient process that utilizes a fiber laser source to cut through metal materials with exceptional precision. The laser beam generated by the fiber laser source is transmitted through an optical fiber, then directed onto the material surface using mirrors and lenses. This straight-cutting process is ideal for a wide range of metals, including steel, stainless steel, aluminum, copper, and brass. Fiber lasers offer high cutting speeds, narrow kerf widths, and minimal heat-affected zones, making them well-suited for industrial applications requiring high accuracy and productivity.

2. Fiber Laser / Plasma Combination: In this cutting process, a combination of fiber laser and plasma cutting technologies is used to achieve versatile cutting capabilities. The fiber laser is primarily utilized for precision cutting of thinner metal sheets, while plasma cutting is employed for thicker materials or when faster cutting speeds are required. This combination approach allows for greater flexibility in handling a wider range of material thicknesses and types. By integrating both laser and plasma cutting technologies into a single machine, manufacturers can optimize cutting efficiency and versatility to meet diverse production needs.
3. Laser Bevel Cutting: Laser bevel cutting is a specialized laser cutting process used to create beveled edges or chamfers on workpiece surfaces. This technique involves tilting the laser beam at an angle relative to the material surface during cutting, resulting in the formation of angled edges along the cut profiles. Laser bevel cutting is commonly used in applications where precise bevel angles and smooth edge transitions are required, such as in the aerospace, automotive, and architectural industries. By adjusting the laser beam angle and cutting parameters, manufacturers can achieve accurate and consistent bevel cuts on various materials, including metals, plastics, and composites.
Each type of laser cutting process offers unique advantages and applications, allowing manufacturers to choose the most suitable method based on their specific requirements for material type, thickness, cutting speed, and edge quality.
What is the laser cutting process?
- Laser Generation: The process begins with the generation of a high-powered laser beam from a laser resonator. The laser beam is typically produced using either a carbon dioxide (CO2) laser or a fiber laser.
- Beam Focusing: The laser beam is then directed through a series of mirrors and lenses to focus it into a concentrated point. This focused beam is extremely intense and precise, allowing it to achieve pinpoint accuracy during cutting or engraving.
- Material Interaction: The focused laser beam is directed onto the surface of the material being processed. When the beam makes contact with the material, it rapidly heats and vaporizes or melts the material along the desired cutting or engraving path.
- Cutting or Engraving: As the laser beam moves along the material, it creates a narrow kerf (cutting path) or removes material layer by layer (engraving). The material either vaporizes and is blown away by assist gases or melts and forms a molten pool, depending on the specific properties of the material and the cutting parameters.
- Motion Control: The laser cutting machine’s motion control system precisely guides the movement of the laser beam across the material, following the programmed cutting or engraving path with high speed and accuracy.
- Cooling and Assist Gas: During the cutting or engraving process, assist gases such as oxygen, nitrogen, or air may be used to aid in material removal and cooling. These gases can help enhance cutting efficiency, improve edge quality, and prevent overheating of the material.
- Finished Product: Once the cutting or engraving process is complete, the finished product is typically removed from the machine. Depending on the application, further processing steps such as cleaning or finishing may be required.
Material handling for laser cutting machines
1. Metal Material types suitable for laser cutting: Laser cutting machines are highly effective for cutting a variety of metal materials, including:
- Steel: Carbon steel, stainless steel, and alloy steel are commonly cut using laser cutting machines. They offer excellent cut quality and are widely used in various industries.
- Aluminum: Aluminum and its alloys are lightweight yet durable materials suitable for laser cutting. They are often used in aerospace, automotive, and architectural applications.
- Copper: While copper is highly reflective to laser beams, fiber lasers are capable of cutting copper materials with precision. Copper is used in electrical and decorative applications.
- Brass: Similar to copper, brass is a metal with high reflectivity, but it can be effectively cut using fiber lasers. Brass is utilized in decorative and artistic projects.
- Titanium: Laser cutting is suitable for processing titanium materials, which are known for their strength, corrosion resistance, and lightweight properties. Titanium is commonly used in aerospace and medical industries.
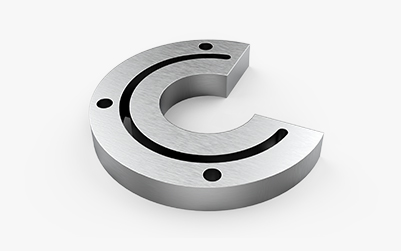
Each metal material may require specific laser cutting parameters, such as laser power, cutting speed, and assist gas selection, to achieve optimal cutting results and minimize heat-affected zones.
2. Effect of material thickness on cutting accuracy: Material thickness plays a significant role in determining cutting accuracy and quality in laser cutting processes:
- Thinner materials typically require lower laser power and faster cutting speeds to achieve precise cuts with minimal distortion.
- Thicker materials may require higher laser power and slower cutting speeds to penetrate through the material effectively and maintain cutting accuracy.
- Material thickness also affects kerf width, which is the width of the cut path. Thicker materials generally result in wider kerf widths, which may impact dimensional accuracy.
To ensure consistent cutting accuracy across different material thicknesses, operators need to adjust cutting parameters accordingly and perform test cuts to optimize settings for each material type.
3. Laser Cutting and Material Compatibility: When it comes to laser cutting, ensuring compatibility between the laser system and the metal material is crucial:
- Reflectivity: Metals with high reflectivity, such as copper and brass, may pose challenges for laser cutting due to beam reflection. Fiber lasers are better suited for cutting reflective metals compared to CO2 lasers.
- Material composition: Some metals contain elements or coatings that may affect laser cutting performance. It’s important to verify material composition and assess compatibility with the laser cutting process.
- Material condition: The condition of the metal material, including surface cleanliness and flatness, can impact cutting quality and consistency. Proper material preparation and handling are essential to achieve optimal laser cutting results.
Laser Cutting Accuracy and Precision
1. Laser cutting accuracy range: Laser cutting machines are renowned for their exceptional accuracy, typically achieving cutting tolerances within a range of ±0.1 mm to ±0.5 mm, depending on various factors such as material type, thickness, and cutting speed. Factors influencing cutting accuracy include the quality of the laser source, the stability of the machine’s motion control system, and the precision of the cutting optics. Advanced laser cutting systems equipped with high-resolution feedback mechanisms and automatic calibration features can further enhance cutting accuracy and consistency.
2. Tips for improving laser cutting accuracy:
- Optimize cutting parameters: Adjust laser power, cutting speed, and assist gas pressure according to the material being processed to achieve optimal cutting results.
- Maintain machine stability: Regularly calibrate and maintain the laser cutting machine to ensure stable operation and minimize vibrations that could affect cutting accuracy.
- Material handling: Properly secure and position the material on the cutting bed to prevent movement or distortion during the cutting process.
- Focus adjustment: Ensure precise focusing of the laser beam onto the material surface to achieve sharp and accurate cuts.
- Quality assurance: Implement quality control measures such as performing test cuts, inspecting finished parts, and monitoring cutting performance to identify and address potential issues affecting accuracy.
3. The difference between accuracy and precision: While accuracy and precision are often used interchangeably, they represent distinct concepts in the context of laser cutting:
- Accuracy refers to the degree of conformity between the actual cutting dimensions and the intended design specifications. It measures how close the achieved results are to the desired outcome.
- Precision, on the other hand, relates to the consistency and repeatability of the cutting process. It quantifies the degree of variation or scatter in the cutting results when repeated under identical conditions.
In essence, accuracy reflects correctness, while precision reflects consistency. A laser cutting process can be accurate but not precise if it consistently produces results that deviate from the intended dimensions by the same amount. Conversely, it can be precise but not accurate if it consistently produces results that cluster tightly around a target point but are consistently offset from the desired dimensions. Ideally, laser cutting systems strive to achieve both high accuracy and precision to ensure reliable and predictable cutting outcomes.
Application scenarios of laser cutting machines
1. Industrial Manufacturing:
- Iron Tower Industry: Laser cutting is used to fabricate precise components for communication towers, transmission towers, and wind turbines.
- Automotive Manufacturing: Laser cutting is employed to produce body panels, chassis parts, and engine components with high precision and efficiency.
- Furniture Industry: Laser cutting enables the fabrication of intricate designs, patterns, and joinery for furniture pieces such as tables, chairs, and cabinets.
- Fitness Equipment: Laser cutting is utilized to manufacture gym equipment such as weight benches, exercise machines, and treadmill components.
- Bicycle Manufacturing: Laser cutting is applied to produce bicycle frames, components, and accessories with lightweight and durable materials.
- Kitchenware Industry: Laser cutting is used to create custom kitchen utensils, cutlery, and appliances from stainless steel, aluminum, and other materials.
- Construction Machinery: Laser cutting is employed to fabricate structural components, frames, and assemblies for construction machinery and equipment.
- Steel Structure Industry: Laser cutting enables the fabrication of steel beams, columns, and trusses for building construction and infrastructure projects.
- Aerospace: Laser cutting is utilized to manufacture aircraft components, engine parts, and aerospace structures with precision and repeatability.
- Environmental Protection Equipment: Laser cutting is applied to produce components for air purification systems, waste management equipment, and renewable energy technologies.
2. Small Businesses and Home Studios:
- Custom Product Manufacturing: Small businesses and home studios use laser cutting to create personalized items such as signage, promotional products, and gifts.
- Crafts and DIY Projects: Hobbyists and DIY enthusiasts utilize laser cutting to craft custom artworks, home decorations, and model kits.
- Prototyping and Product Development: Entrepreneurs and inventors leverage laser cutting for rapid prototyping and iterative design processes to bring new products to market.
3. Education and Hobbyists:
- STEM Education: Laser cutting is integrated into STEM curricula to teach students about engineering, design, and manufacturing principles through hands-on projects.
- Art and Design: Artists and designers use laser cutting to explore new forms of artistic expression, creating sculptures, installations, and mixed-media artworks.
- Model Making and Prototyping: Hobbyists and enthusiasts utilize laser cutting to build scale models, replicas, and prototypes of vehicles, buildings, and other objects of interest.
In summary, laser cutting machines find diverse applications across industrial manufacturing, small businesses, home studios, education, and hobbyist communities, enabling precision, efficiency, and creativity in a wide range of industries and pursuits.
Laser cutting machine operation and maintenance
1. Daily operation process of laser cutting machine:
- Power On: Ensure the laser cutting machine is properly connected to power and switch it on following manufacturer guidelines.
- Material Setup: Prepare the material to be cut or engraved, ensuring it is securely positioned on the cutting bed and aligned correctly.
- Machine Setup: Set cutting parameters such as laser power, cutting speed, and assist gas pressure according to material type and thickness.
- File Loading: Load the desired design file into the laser cutting software and verify settings before initiating the cutting process.
- Safety Precautions: Wear appropriate personal protective equipment (PPE) such as safety glasses and gloves, and ensure the work area is clear of obstructions.
- Cutting Process: Start the cutting process using the control panel or software interface, monitoring the operation to ensure proper cutting quality and accuracy.
- Post-Processing: Remove finished parts from the cutting bed, inspect for quality, and perform any necessary post-processing steps such as cleaning or deburring.
2. Laser Cutting Machine Maintenance and Troubleshooting:
- Regular Cleaning: Clean the laser optics, cutting head, and cutting bed regularly to remove debris and ensure optimal performance.
- Lubrication: Lubricate moving parts such as guide rails and ball screws according to manufacturer recommendations to prevent wear and friction.
- Inspect Consumables: Check consumable parts such as lenses, nozzles, and assist gas filters for signs of wear or damage, replacing them as needed.
- Calibration: Periodically calibrate the laser cutting machine to maintain cutting accuracy and alignment of components.
- Troubleshooting: In case of issues such as cutting defects, machine errors, or malfunctions, refer to the manufacturer’s troubleshooting guide or consult qualified technicians for assistance.
- Emergency Procedures: Familiarize yourself with emergency shutdown procedures and safety protocols in case of accidents or emergencies.
3. User Training and Safe Operating Guide:
- Training: Provide comprehensive training to machine operators on safe operating procedures, machine controls, and maintenance tasks before allowing them to operate the laser cutting machine independently.
- Safety Guidelines: Emphasize the importance of following safety guidelines, including wearing appropriate PPE, avoiding contact with moving parts, and keeping hands clear of the cutting area during operation.
- Ventilation and Extraction: Ensure adequate ventilation and extraction systems are in place to remove fumes, smoke, and particulates generated during the cutting process.
- Emergency Stop: Locate and familiarize users with the emergency stop button or switch to immediately halt machine operation in case of emergencies.
If there is any machine related issue about install and use, the JQ laser support team is always available.
Technological Advances in Laser Cutting Machines
1. Developments in Latest Laser Cutting Technology:
- Fiber Laser Technology: Continued advancements in fiber laser technology have led to higher power densities, improved beam quality, and enhanced cutting capabilities. Fiber lasers offer greater energy efficiency, faster cutting speeds, and increased reliability compared to traditional CO2 lasers.
- High-Precision Cutting: Advanced laser cutting systems incorporate features such as adaptive optics, beam shaping, and real-time monitoring to achieve micron-level precision and edge quality, enabling ultra-precise cutting of intricate geometries and thin materials.
- Multi-Material Cutting: Laser cutting machines are becoming increasingly versatile, capable of processing a wider range of materials including metals, composites, ceramics, and organic materials with minimal setup and tooling changes.
- Integrated Sensing and Feedback: Integration of sensors, cameras, and feedback systems enables real-time monitoring of cutting processes, material properties, and machine performance, allowing for adaptive control and optimization of cutting parameters.
- Additive Manufacturing Integration: Integration of laser cutting with additive manufacturing technologies such as 3D printing enables hybrid manufacturing processes that combine subtractive and additive techniques for greater design freedom and part complexity.
2. Automation and Intelligence of Laser Cutting Machines:
- Automated Material Handling: Laser cutting systems are equipped with automated loading/unloading systems, material handling robots, and pallet changers to streamline production workflows, reduce downtime, and increase throughput.
- Smart Control Systems: Advanced control software with AI algorithms, machine learning, and predictive analytics optimize cutting parameters, tool paths, and maintenance schedules to maximize efficiency, productivity, and material utilization.
- Remote Monitoring and Diagnostics: Cloud-based connectivity and IoT-enabled sensors allow operators to remotely monitor machine performance, receive real-time alerts, and troubleshoot issues, enhancing operational visibility and uptime.
- Intelligent Part Nesting: AI-driven nesting algorithms optimize material utilization by arranging parts on the cutting bed for maximum efficiency, minimizing scrap and reducing material waste.
- Autonomous Maintenance: Self-diagnostic capabilities and predictive maintenance algorithms automatically detect and address potential issues before they lead to downtime, improving overall equipment effectiveness (OEE) and reducing maintenance costs.
3. Future Trends in Laser Cutting Technology:
- Ultrafast Lasers: Advancements in ultrafast laser technology enable precision cutting of heat-sensitive materials with minimal thermal damage, opening up new opportunities in microfabrication, electronics, and medical device manufacturing.
- High-Power Lasers: Continued development of high-power lasers with kilowatt-level outputs enables rapid cutting of thick materials, expanding the range of applications in heavy industry, shipbuilding, and infrastructure.
- Hybrid Laser Systems: Integration of laser cutting with other machining processes such as milling, drilling, and welding into hybrid manufacturing systems offers greater versatility, flexibility, and cost-effectiveness for complex part production.
- Green Laser Technology: Emerging green laser sources with shorter wavelengths and higher absorption rates in certain materials provide new possibilities for ultra-precise cutting of transparent materials, ceramics, and semiconductors.
- 3D Laser Cutting: Advancements in 3D laser cutting technology enable the fabrication of complex three-dimensional parts and assemblies with high accuracy and efficiency, revolutionizing applications in automotive, aerospace, and medical industries.
Laser cutting machine software and control system
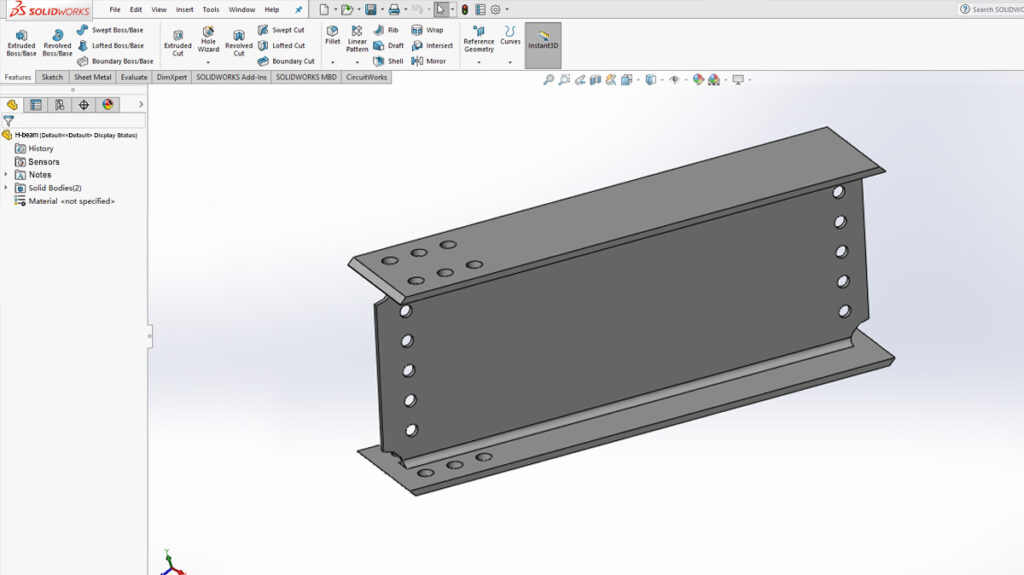
1. Control software options for laser cutting machines:
- Proprietary Software: Many laser cutting machine manufacturers offer their own proprietary control software tailored specifically for their machines. Proprietary software from laser machine manufacturers like TRUMPF, Siemens, and Weihong. These software solutions typically provide comprehensive control over cutting parameters, tool paths, and machine functions.
- Third-party Software: Alternatively, users may opt for third-party control software solutions that offer compatibility with a wide range of laser cutting machines. These software packages often feature advanced capabilities such as nesting, optimization, and integration with CAD/CAM software.
2. Application of CAD/CAM software in laser cutting:
- CAD Software: Computer-Aided Design (CAD) software is used to create precise digital models of parts and components to be manufactured. CAD software allows designers to create and modify designs with precision and accuracy, which can then be exported to CAM software for toolpath generation.
- CAM Software: Computer-Aided Manufacturing (CAM) software converts CAD designs into machine-readable instructions for the laser cutting machine. CAM software generates toolpaths, optimizes cutting sequences, and assigns cutting parameters based on material properties and machine capabilities. Advanced CAM software packages offer features such as nesting, automatic part orientation, and simulation to maximize efficiency and material utilization.
3. The impact of software on cutting accuracy:
- Precision Control: Laser cutting machine software plays a crucial role in determining cutting accuracy by controlling factors such as laser power, cutting speed, focal length, and assist gas pressure. Fine-tuning these parameters with precision can significantly impact the quality and accuracy of the cut.
- Path Optimization: Advanced software solutions employ algorithms to optimize cutting paths, minimize toolpath length, and reduce unnecessary movements, leading to smoother cuts, sharper corners, and improved accuracy.
- Simulation and Verification: Some software packages offer simulation and verification tools that allow users to visualize cutting paths, detect potential collisions, and identify areas of concern before initiating the cutting process. This helps prevent errors and ensures accurate results.
- Integration with Feedback Systems: Integration with feedback systems and sensors enables real-time monitoring of cutting processes, material properties, and machine performance. This feedback loop allows the software to make adjustments on the fly to maintain cutting accuracy and quality.
Laser cutting machine design and customization
1. Considerations for Custom Laser Cutting Machines:
- Material Compatibility: Custom laser cutting machines should be designed to accommodate a wide range of materials, including metals, plastics, woods, and composites. Considerations such as bed size, laser power, and cutting capabilities should be tailored to the specific materials and applications intended for use.
- Flexibility and Versatility: Custom machines should offer flexibility to adapt to different cutting requirements and production needs. This may include adjustable settings for laser power, cutting speed, focal length, and assist gas pressure to optimize cutting performance for various materials and thicknesses.
- Integration with Workflow: Custom laser cutting machines should seamlessly integrate into existing workflow processes, production lines, and automation systems. Considerations such as material handling, loading/unloading mechanisms, and workflow automation should be incorporated into the design to streamline operations and maximize efficiency.
- Safety and Ergonomics: Safety features such as interlocks, enclosures, and protective barriers should be integrated into the design to ensure operator safety and compliance with regulatory standards. Ergonomic considerations such as accessibility, ease of maintenance, and operator comfort should also be taken into account to enhance usability and user experience.
2. Personalization and Additional Functions for Laser Cutting Machines:
- Customizable Features: Laser cutting machines can be customized with additional features and functionalities to meet specific user requirements and preferences. This may include options for rotary attachments, dual-head configurations, vision systems, and automatic nozzle changers to expand capabilities and enhance productivity.
- Software Integration: Personalization options may include integration with specialized software tools for CAD/CAM, nesting, and workflow management to streamline design-to-cut processes and optimize production efficiency.
- Accessory Compatibility: Laser cutting machines can be designed to be compatible with a variety of accessories and add-ons such as rotary attachments for cylindrical engraving, autofocus systems for precise focusing, and conveyor systems for continuous material processing.
3. The Impact of Design on Laser Cutting Accuracy:
- Structural Rigidity: The design of the laser cutting machine frame and gantry structure plays a critical role in maintaining cutting accuracy. A rigid and stable frame minimizes vibration and deflection during cutting, ensuring consistent cutting performance and dimensional accuracy.
- Motion Control System: Precision motion control components such as linear guides, ball screws, and servo motors should be carefully selected and integrated into the machine design to minimize backlash, friction, and positioning errors, thereby enhancing cutting accuracy.
- Optical System: The design and alignment of the laser beam delivery system, including mirrors, lenses, and focusing optics, directly impact cutting accuracy. Proper calibration and maintenance of the optical system are essential to ensure precise beam delivery and consistent cutting results.
- Cooling and Environmental Control: Temperature and environmental conditions can affect laser performance and cutting accuracy. Laser cutting machines should be equipped with effective cooling systems and environmental controls to maintain stable operating conditions and prevent thermal drift, particularly in high-precision applications.
Environmental and safety standards for laser cutting machines
1. Environmental Impact of Laser Cutting Machines:
- Air Quality: Laser cutting machines produce emissions such as fumes, smoke, and particulates during the cutting process, which can impact indoor air quality and pose health risks to operators. Proper ventilation and filtration systems are essential to minimize air pollution and ensure a safe working environment.
- Energy Consumption: Laser cutting machines consume electricity to power the laser source, motion control systems, and auxiliary components. Energy-efficient design and operation, as well as the use of renewable energy sources, can help reduce the environmental footprint of laser cutting operations.
- Material Waste: Laser cutting processes generate waste materials such as offcuts, scrap, and dust, which may require proper disposal or recycling to minimize environmental impact. Optimization of cutting parameters, nesting algorithms, and material utilization can help reduce waste generation and improve resource efficiency.
2. Safety Standards and Certifications for Laser Cutting Machines:
- International Standards: Laser cutting machines are subject to international safety standards and regulations, such as IEC 60825 for laser safety and ISO 13849 for machinery safety. Compliance with these standards ensures that laser cutting machines meet minimum safety requirements for operation and mitigate potential hazards.
- CE Marking: Laser cutting machines intended for sale within the European Economic Area (EEA) must comply with the CE marking requirements, which demonstrate conformity with applicable EU directives related to safety, health, and environmental protection.
- UL Listing: In North America, laser cutting machines may undergo testing and certification by organizations such as Underwriters Laboratories (UL) to ensure compliance with safety standards and requirements for electrical safety and fire protection.
3. Health and Safety Operating Guidelines for Laser Cutting Machines:
- Operator Training: Operators should receive comprehensive training on safe operating procedures, laser safety principles, and emergency protocols before using laser cutting machines. Training should cover topics such as proper PPE usage, machine controls, material handling, and maintenance tasks.
- Personal Protective Equipment (PPE): Operators should wear appropriate PPE such as safety glasses, gloves, and hearing protection to minimize exposure to laser radiation, fumes, and noise generated during cutting operations.
- Machine Guarding: Laser cutting machines should be equipped with safety features such as interlocks, enclosures, and protective barriers to prevent access to hazardous areas and mitigate the risk of injury from moving parts, laser beams, and flying debris.
- Emergency Procedures: Emergency stop buttons, alarms, and evacuation procedures should be clearly identified and accessible to operators in case of accidents, malfunctions, or other emergencies requiring immediate intervention.
Laser Cutting Considerations
Let’s explore key considerations in laser cutting:
1. Focal Spot:
- The focal spot refers to the area where the laser beam converges to its smallest diameter. A smaller focal spot size results in higher intensity, allowing for finer and more precise cuts. The focal spot size is influenced by factors such as the focusing lens and beam quality.
2. Beam Mode:
- The beam mode describes the spatial distribution of the laser beam’s intensity profile. Different beam modes, such as Gaussian, TEM00 (fundamental mode), and multimode, affect cutting characteristics such as beam divergence, depth of focus, and cutting efficiency. Choosing the appropriate beam mode depends on the specific cutting requirements and material properties.
3. Laser Power:
- Laser power refers to the amount of energy delivered by the laser beam per unit of time. Higher laser power allows for faster cutting speeds and increased penetration depth, particularly for thicker materials. However, excessive power can lead to thermal damage, distortion, and rough edges, so it’s essential to balance power with cutting quality and material compatibility.
4. Machine Configuration:
- Laser cutting machines come in various configurations, including CO2 and fiber lasers, flatbed and gantry designs, and hybrid systems with additional machining capabilities. The choice of machine configuration depends on factors such as material type, thickness, cutting speed requirements, and budget constraints. Considerations such as bed size, positioning accuracy, and auxiliary features (e.g., automatic nozzle changers, rotary axes) also influence machine selection.
5. Material Considerations:
- Different materials exhibit varying responses to laser cutting, including factors such as absorption, reflectivity, thermal conductivity, and melting point. It’s essential to consider material properties such as composition, thickness, surface finish, and tolerance requirements when selecting cutting parameters and machine settings. Some materials may require special handling or auxiliary processes (e.g., assist gas, preheating) to achieve optimal cutting results and minimize defects.
Conclusión
In conclusion, the comprehensive laser cutting machine guide offers a detailed insight into the technology, processes, and important factors to consider when using this powerful tool. It covers everything from the basic principles of laser cutting to advanced techniques and applications, making it a valuable resource for both novices and experienced operators.
Another guide for tube laser machine: Unlimited guide of tube laser cutting
Deja una respuesta