Laser cutting technology has revolutionized the manufacturing industry, providing precise and efficient methods for cutting various types of metals. One of the most critical factors influencing the effectiveness of laser cutting is the relationship between the power of the laser and the thickness of the metal being cut. Understanding this relationship is essential for optimizing cutting processes and achieving high-quality results.
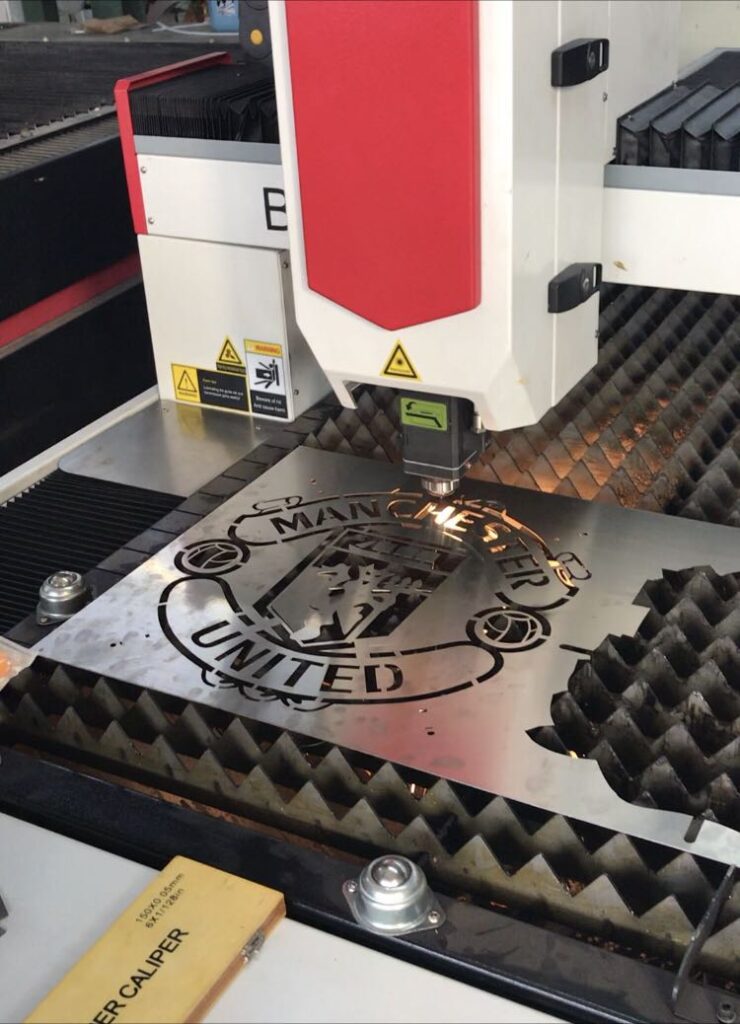
1. Understanding Laser Power
Laser power, measured in watts (W), is a key determinant of a laser cutting machine’s capability. Higher power levels allow for faster cutting speeds and the ability to cut through thicker materials.
- Power Ratings: Common power ratings for laser cutting machines range from 500W to 80,000W. Each increment in power typically corresponds to an increase in the maximum thickness of metal that can be effectively cut.
- Types of Lasers: Different types of lasers, such as CO2 and fiber lasers, exhibit varying efficiencies and cutting capabilities based on their power output. Fiber lasers are generally more efficient for cutting metals than CO2 lasers at equivalent power levels.
By understanding how laser power affects cutting capabilities, operators can select appropriate machines for their specific applications.
2. Cutting Thickness by Power Level
The thickness of metal that can be cut by a laser machine increases with higher power levels. Below is a general overview of how different power ratings correspond to maximum cutting thickness for various metals:
- 500W Laser:
- Carbon Steel: Up to 6 mm
- Stainless Steel: Up to 3 mm
- Aluminum: Up to 2 mm
- 1000W Laser:
- Carbon Steel: Up to 10 mm
- Stainless Steel: Up to 5 mm
- Aluminum: Up to 3 mm
- 3000W Laser:
- Carbon Steel: Up to 20 mm
- Stainless Steel: Up to 10 mm
- Aluminum: Up to 8 mm
- 6000W Laser:
- Carbon Steel: Up to 30 mm
- Stainless Steel: Up to 20 mm
- Aluminum: Up to 20 mm
- 12000W Laser:
- Carbon Steel: Up to 35 mm
- Stainless Steel: Up to 30 mm
- Aluminum: Up to 30 mm
- 20000W Laser:
- Carbon Steel: Up to 60 mm
- Stainless Steel: Up to 50 mm
- Aluminum: Up to 40 mm
These values indicate that as laser power increases, so does the maximum thickness of metal that can be cut effectively.
3. Factors Influencing Cutting Thickness
While laser power is a significant factor, other variables also play crucial roles in determining cutting thickness:
- Material Type: Different metals have unique properties such as reflectivity, melting points, and thermal conductivity, which affect how well they can be cut by lasers. For instance, aluminum has high reflectivity, requiring higher power levels for effective cutting compared to carbon steel.
- Vitesse de coupe: The speed at which the laser moves during cutting also impacts thickness capabilities. Slower speeds allow for deeper penetration into thicker materials but may lead to heat buildup if not managed properly.
- Focal Length and Lens Quality: The focal length of the lens used in the laser cutter affects beam focus and intensity. A well-focused beam can achieve cleaner cuts even at greater thicknesses.
- Gas Type and Pressure: The type of assist gas (such as oxygen or nitrogen) used during cutting can influence the quality and speed of cuts. Higher pressure gases can enhance cutting efficiency but may require adjustments in power settings.
By considering these factors alongside laser power, operators can optimize their cutting processes for specific materials and applications.
4. Practical Applications in Industry
Understanding the relationship between laser power and metal cutting thickness is vital across various industries:
- Fabrication: In manufacturing settings, selecting the right laser cutter based on material thickness requirements can streamline production processes and improve efficiency.
- Aerospace and Automotive: Industries that require precise cuts in thick metals often rely on high-power lasers (20kW or higher) for tasks such as structural component fabrication.
- Art and Design: In artistic applications, knowledge of cutting capabilities allows designers to create intricate patterns in various metal substrates without compromising quality.
By applying this understanding effectively, businesses can enhance their operational efficiency while maintaining high standards of quality.
Conclusion
The relationship between laser power and metal cutting thickness is fundamental in optimizing laser cutting operations. Higher power levels enable the effective cutting of thicker materials while also influencing speed and quality. By understanding this relationship along with other contributing factors—such as material type, cutting speed, and equipment specifications—operators can make informed decisions that enhance productivity and ensure superior results in their metal fabrication processes. Whether in manufacturing or artistic applications, leveraging this knowledge will lead to better outcomes and greater satisfaction among clients.