In the modern job shop, laser and TIG welding coexist as complementary techniques, each offering unique advantages that cater to different needs within the fabrication process. The integration of these two methods allows job shops to maximize efficiency, precision, and versatility, addressing a wide range of welding requirements.Laser welding is renowned for its precision and speed. It uses a focused laser beam to join materials, creating a small heat-affected zone and allowing for high-quality welds with minimal distortion. This method is particularly advantageous for applications requiring tight tolerances and high-speed production, such as in the aerospace, electronics, and automotive industries. On the other hand, TIG welding, which stands for Tungsten Inert Gas welding, is highly valued for its versatility and ability to handle a variety of metals and thicknesses. It is a slower process compared to laser welding but offers greater control, making it ideal for intricate and detailed work.
Comparison of Laser and TIG Welding
Feature | Laser Welding | TIG Welding |
---|---|---|
Precision | High precision with minimal heat-affected zone | High control, suitable for intricate welds |
Speed | Faster than TIG, ideal for high-volume production | Slower, allows for detailed and controlled welding |
Material Compatibility | Suitable for thin metals and dissimilar materials | Versatile, works with a wide range of metals |
Automation | Easily automated, integrates with CNC systems | Less suitable for automation due to manual control |
Heat Generation | Low, reducing the risk of distortion | Higher, can lead to more distortion |
Cost | Higher initial investment, lower operational costs | Lower initial cost, higher operational costs |
Laser welding’s ability to automate and integrate with CNC systems makes it a popular choice for mass production environments. Its precision and speed are unmatched, allowing for efficient production cycles and high-quality outputs. However, the initial investment for laser welding equipment can be substantial, which may be a barrier for smaller shops.TIG welding, while slower, provides unmatched control over the welding process. This makes it ideal for applications where precision and detail are paramount, such as artistic metalwork or complex assemblies. The versatility of TIG welding in handling various metals and thicknesses also makes it indispensable in many job shops.
The Role of Automation and Innovation
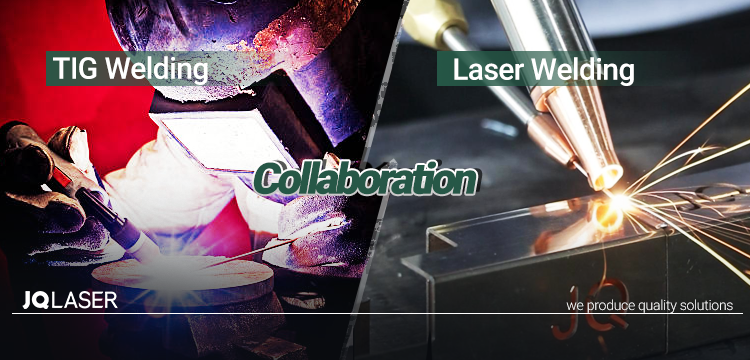
The rise of automation in welding has significantly influenced how laser and TIG welding are utilized. Laser welding, with its ease of automation, is often used in robotic welding systems, enhancing productivity and consistency in high-volume production settings. This automation capability allows job shops to allocate skilled welders to more complex tasks, optimizing resource utilization.Innovation in welding technology has also expanded the capabilities of both laser and TIG welding. Advances in laser technology, such as fiber lasers, have reduced costs and increased accessibility, making laser welding a viable option for more applications. Similarly, improvements in TIG welding equipment have enhanced its efficiency and ease of use, further solidifying its role in the modern job shop.
Applications and Industry Impact
The coexistence of laser and TIG welding in job shops has broadened the scope of applications across various industries. In the aerospace sector, the precision of laser welding is crucial for manufacturing components with stringent tolerances. In contrast, TIG welding is often employed for its ability to handle complex geometries and thicker materials.In the automotive industry, both welding methods are used to meet the demands for lightweight and durable components. Laser welding’s speed and precision are ideal for high-volume production of thin metal parts, while TIG welding’s versatility is essential for assembling more intricate structures.The electronics industry benefits from laser welding’s ability to join small and delicate components without damaging surrounding areas. Meanwhile, TIG welding is used for tasks requiring detailed manual control, such as repairing or modifying existing assemblies.
- Aerospace Industry: Laser welding is extensively used for manufacturing components that require high precision and minimal distortion. For instance, it is employed in welding turbine blades and fuselage sections, where the precision and low heat input of laser welding ensure structural integrity and performance.
- Automotive Sector: In automotive manufacturing, laser welding is utilized for body-in-white components, which are the primary structural parts of a vehicle. The high-speed and automated nature of laser welding make it ideal for mass production of car frames and panels. TIG welding, on the other hand, is used for more intricate tasks such as assembling exhaust systems and fuel tanks, where its versatility and control are beneficial.
- Medical Devices: The medical industry benefits from laser welding’s precision for assembling complex devices like surgical instruments and implants. For example, laser welding is used for the hermetical sealing of titanium shells enclosing medical implants, ensuring sterility and precision.
- Electronics Industry: Laser welding is favored for joining delicate electronic components, such as circuit boards and sensors, due to its ability to produce high-quality welds without damaging sensitive parts. This application is crucial in maintaining the functionality and reliability of electronic devices.
- Jewelry Manufacturing: In the jewelry industry, laser welding is employed for intricate designs that require fine detail and precision. The minimal heat-affected zone ensures that the delicate metals used in jewelry are not damaged during the welding process.
- Electric Vehicles (EVs): A notable case study involves the use of laser welding for joining copper busbars to battery tabs in electric vehicles. This application highlights the efficiency and precision of laser welding in meeting the demands of high-quality and fast-paced production environments.
- Tooling and Repair: Laser welding is also used for tooling revision and repair, such as fixing worn-out molds and dies. Its precision allows for targeted repairs without affecting the surrounding areas, extending the lifespan of expensive tooling equipment.
These examples demonstrate how laser and TIG welding complement each other in various industries, with laser welding often taking the lead in high-speed and precision applications, while TIG welding provides the versatility and control needed for more intricate and detailed work. This synergy allows job shops to tackle a wide range of welding challenges, enhancing their capability to deliver high-quality products across different sectors.
Future Trends and Developments
As technology continues to evolve, the integration of laser and TIG welding in job shops is expected to become even more seamless. The development of hybrid welding systems that combine the strengths of both methods is a promising trend, offering enhanced flexibility and efficiency. Additionally, advancements in digitalization and robotics are likely to further improve the precision and automation capabilities of welding processes.The emphasis on sustainability and energy efficiency is also driving innovation in welding technology. Both laser and TIG welding are being optimized to reduce energy consumption and minimize waste, aligning with the growing demand for environmentally friendly manufacturing practices.In conclusion, the coexistence of laser and TIG welding in the modern job shop exemplifies the synergy between precision, speed, and versatility. By leveraging the strengths of both methods, job shops can address a diverse array of welding challenges, ensuring high-quality outputs and efficient production processes. As technology continues to advance, the role of these welding techniques in shaping the future of manufacturing is set to expand even further.