Intelligent feeding system
The feeding side is designed with an intelligent chain feeding system. The system adopts the front-aligning method to place the raw materials in the vacant positions of the feeding rack chain in sequence. The feeding system uses servo control to transport the materials on the chain to the main machine feeding area, and then controls the support device to rise through the servo system. The raw materials are lifted to a suitable height through servo positioning control, and the raw materials are automatically centered and then transported to the chuck clamping position through servo positioning control; during the motion control process, the servo control uses the encoder for positioning, and there are mechanical limits at both ends to ensure the safety of system operation.
The feeding rack can be equipped with a storage area (optional) to store a certain amount of raw materials according to material specifications, improve feeding efficiency, and reduce manual labor intensity.
Intelligent unloading system
Flip plate unloading
It has a flipping function, which is realized by the solenoid valve controlling the cylinder; the cut workpiece can be flipped onto the storage rack, and the workpiece slides out sideways along the storage rack.
Chain unloading
After the workpiece is cut, it can be dropped onto the unloading rack chain and then transported to an empty workstation for temporary storage. The entire conveying process is smooth and orderly with less impact.
During the processing, the system will control the follow-up material receiving device to adjust the material receiving height of the receiving component in real time according to the changes in the outer contour of the material, so as to ensure that the receiving plate stably supports the pipe. When the chuck moves to the corresponding position, the follow-up material receiving device will automatically drop to avoid it.
After the workpiece is processed, the system will intelligently judge the material unloading area according to the length of the unloading workpiece. Different material lengths will have different corresponding programs, which are compatible with unloading efficiency and unloading stability. When the last section of the workpiece meets the shortest length specified in the technical requirements, zero tail material cutting can be achieved.
Recommended Products
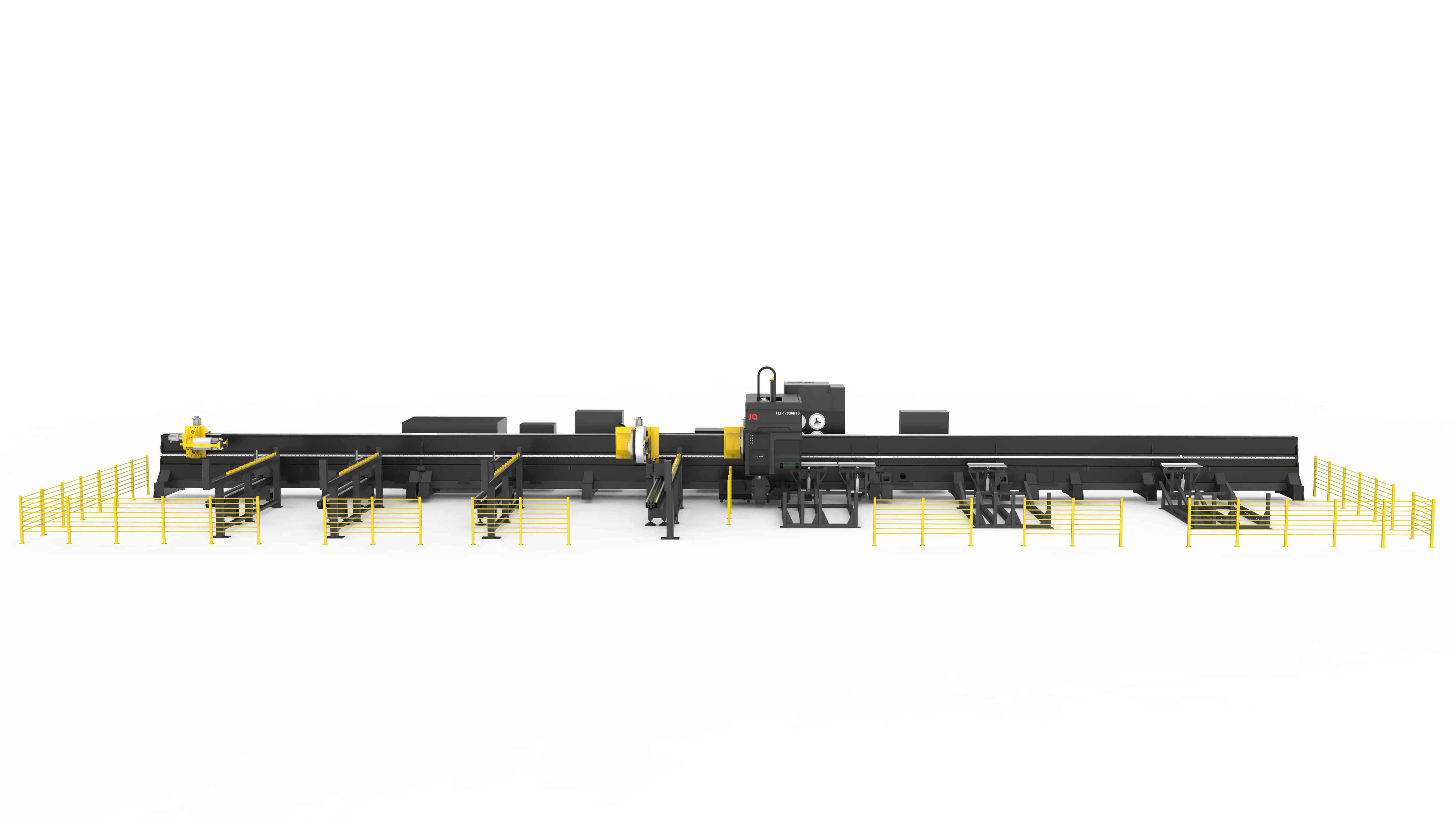
FLT-12036HT