Introduction: Embracing Modern Welding Techniques
In the realm of manufacturing and construction, the utilization of cutting-edge welding techniques has become pivotal in ensuring superior structural integrity and efficiency. Laser welding and MIG (Metal Inert Gas) welding stand out as two prominent methods revolutionizing the welding industry, each with its unique features and applications. Understanding the distinctions and benefits of these methods is vital for industries seeking to enhance their production capabilities and ensure top-notch weld quality.
Laser Welding: Precision and Versatility in Manufacturing
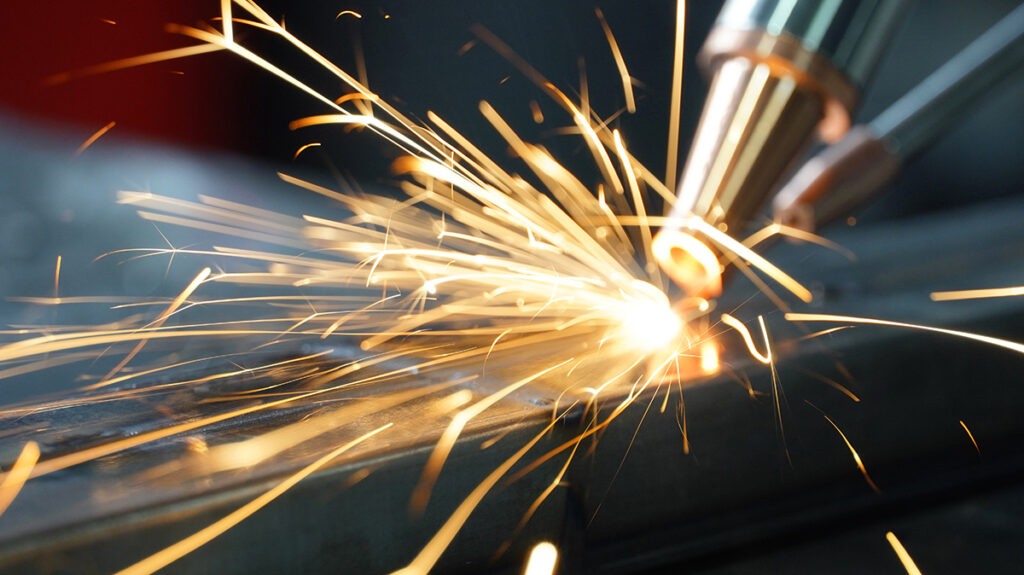
Laser welding, a state-of-the-art technique, has gained significant traction in various industries due to its unparalleled precision and versatility. By harnessing the power of focused light beams, this method enables the welding of complex geometries with exceptional accuracy and minimal heat distortion. Industries such as automotive, aerospace, and electronics have embraced laser welding for its ability to handle delicate materials and create seamless, high-quality welds. Moreover, its non-contact nature minimizes the risk of contamination, making it ideal for industries with stringent hygiene standards.
MIG Welding: Efficiency and Adaptability in Industrial Fabrication
On the other hand, MIG welding, also known as Gas Metal Arc Welding (GMAW), has established itself as a go-to method for industrial fabrication processes. Offering high levels of efficiency and adaptability, MIG welding utilizes a consumable electrode to create strong and robust welds in various materials, including stainless steel, aluminum, and mild steel. Its ease of use and cost-effectiveness have made it a preferred choice for large-scale production environments, where speed and consistent weld quality are paramount.
Key Differences and Comparative Advantages
When comparing laser welding and MIG welding, it’s crucial to acknowledge their fundamental differences and relative advantages. Laser welding excels in precision, enabling intricate welding tasks with minimal heat-affected zones, making it ideal for applications requiring minimal post-weld processing. Conversely, MIG welding’s adaptability and speed make it suitable for high-volume production, where swift welding operations are essential. Understanding the specific requirements of each project is imperative in determining which technique aligns best with the desired outcomes.
Optimizing Welding Processes for Enhanced Productivity and Quality
To maximize the benefits of both laser welding and MIG welding, industries can adopt a strategic approach that integrates the strengths of each technique. Incorporating laser welding for intricate components and critical joints can ensure unparalleled accuracy and structural integrity. Simultaneously, leveraging MIG welding for large-scale production lines can boost efficiency and output without compromising on weld quality. By employing a hybrid welding approach tailored to the specific demands of a project, businesses can optimize their welding processes and elevate their overall productivity and quality standards.
Conclusion: A Holistic Approach to Welding Excellence
In the dynamic landscape of modern manufacturing, the choice between laser welding and MIG welding relies on a comprehensive understanding of their capabilities and applications. While laser welding caters to intricate and precise welding needs, MIG welding thrives in high-volume, cost-effective production environments. By leveraging the strengths of both methods and integrating them judiciously, industries can achieve optimal welding results, enhancing product quality, and maintaining a competitive edge in today’s demanding market.
In embracing the diversity of welding techniques, industries can pave the way for innovation, efficiency, and excellence in their manufacturing processes, driving the progress of various sectors and shaping a future defined by superior welding capabilities and breakthrough technological advancements.