Exploring the Working Principles of Tube Laser Cutting Machines
Tube laser cutting machines revolutionized the manufacturing industry by providing faster and more accurate ways to cut cylindrical and square tubes with different thicknesses. This technology employs fiber optics or CO2 lasers that cut the tubes with precision, making them ideal for manufacturing applications that require high precision and exact measurements.
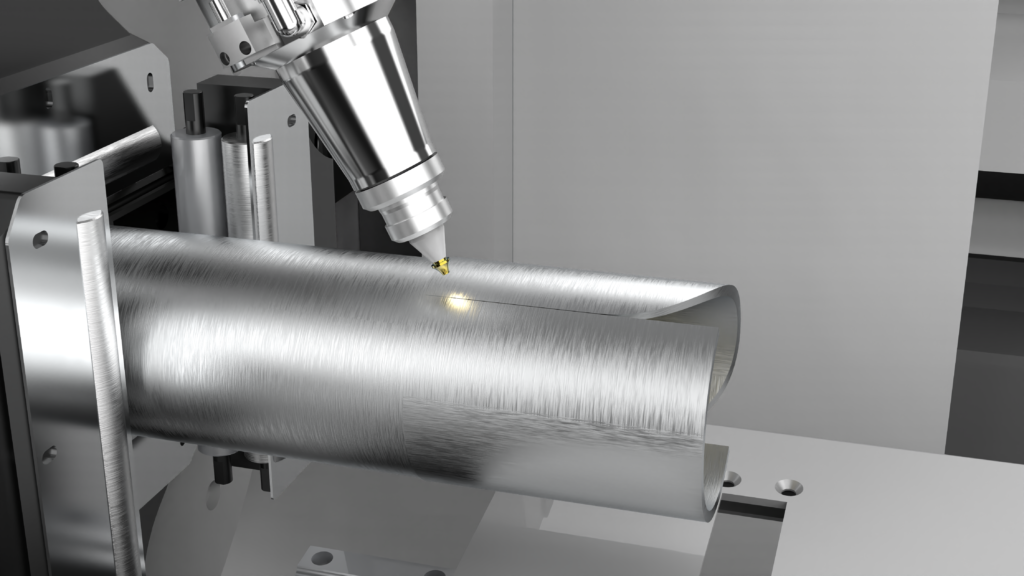
The Laser Source
At the heart of any laser cutting machine is the laser source itself. This source generates an intense, focused beam of light, typically a CO2 laser or a fiber laser, which is the key element responsible for the cutting process.
Material Loading
Before the cutting can begin, metal tubes must be loaded into the machine. This step is crucial as it determines the alignment and positioning of the tubes, ensuring accuracy throughout the process.
Precision Focusing
The laser beam is then precisely focused on the surface of the metal tube. This focus is vital in achieving clean and accurate cuts, especially for intricate designs and complex shapes.
The Cutting Process
With the laser beam focused, the cutting process begins, and this is where the magic truly happens.
Material Interaction
As the high-energy laser beam makes contact with the metal surface, it rapidly heats the material. This heating leads to vaporization, melting, or even combustion of the metal, depending on the material and thickness.
Assist Gas
To enhance the cutting process, assist gases such as nitrogen or oxygen are often used. These gases help blow away the molten metal, ensuring a clean and precise cut.
Computer Numerical Control (CNC)
Tube laser cutting machines are guided by CNC systems, which follow a pre-programmed design or pattern with pinpoint accuracy. This technology allows for the creation of intricate cuts and complex shapes.
The Efficiency of Tube Laser Cutting: How it Works
The efficiency of tube laser cutting is attributed to the high power and speed of the laser beams, which allow for accurate cuts at high speeds. The machines use a combination of cutting gas, a laser beam, and advanced computer software to achieve efficient and high-quality cuts. The laser cuts the metal in the tube, while the cutting gas removes the molten material and protects the cut from impurities.
The Advantages of Tube Laser Cutting Machines
- High precision cutting with less waste material
- Cuts through different metals, including steel, stainless steel, and aluminum
- Reduces setup time and labor costs
- High cutting speeds and better production rates
- Burr-free cuts with clean and smooth edges
The Role of Fiber Optics in Enhancing the Laser Cutting Process
The use of fiber optics in tube laser cutting machines allows for increased cutting efficiency and better performance. Fiber lasers are faster, more efficient, and more reliable than CO2 lasers. They also require less maintenance and last longer. The fiber optics also reduce the maintenance of reflective mirrors, which helps in maintaining the quality of the cutting machine.
The Use of CO2 Lasers in Tube Laser Cutting
CO2 lasers were the first type of lasers used in tube laser cutting machines. They operate on a mixture of carbon dioxide, nitrogen, and helium gas, and they emit an infrared beam with a wavelength of about 10 micrometers. CO2 lasers work well with non-metallic materials and are suitable for heavy-gauge metals, but they are less efficient than fiber lasers in thin metal sheets.
The Importance of Accurate Measurements in Tube Laser Cutting
Accurate measurement is an essential aspect of tube laser cutting machines since the machines operate based on pre-programmed paths. Precise measurement means that the laser cuts the tube at the right position, length, and angle, ensuring that the final product is accurate and of high quality.
The Evolution of Tube Laser Cutting Machines: Past, Present, and Future

The tube laser cutting machine has come a long way since its inception. The earliest models were large and slow, and they only operated on CO2 lasers. However, today’s models are faster, more accurate, and rely mainly on fiber-optic lasers. The future of these machines is likely to involve even faster cutting speeds, increased productivity, and more automated features.
The Impact of Automated Features on the Industry
The introduction of automation features, such as robotic arms, automatic loading and automatic unloading, has had a significant impact on manufacturing. These features reduce labor costs, increase productivity, and reduce setup time. They also reduce the potential for errors and improve cutting accuracy.
According to a recent BCG study, closing this “automation gap” can achieve labor and quality improvements, reducing conversion costs by as much as 25 percent. However, changes in mechatronic systems, such as robots, are only part of the solution. Manufacturers must also change their products, organizations and IT setups to achieve higher levels of automation.
However, digital automation since the 1980s has increased labor market inequality, as many production and clerical workers have seen their jobs disappear or their wages drop. And of course new jobs have been created.
Industrial robotics is an automation technology that may lead to structural changes in the labor market, especially in routine manual work. The use of robots has expanded globally. In the United States, there were 1.79 robots per 1,000 workers in 2017, compared to 0.49 robots per 1,000 workers in 1995.
In short, automation features have had a broad impact on manufacturing. They bring many advantages to companies, such as reduced costs and increased productivity and accuracy. However, automation has also created structural changes in the labor market that could lead to the disappearance of certain jobs. Manufacturers and policy makers need to pay close attention to the development of automation and develop appropriate strategies to address these changes.
The Role of Software in Enhancing Tube Laser Cutting Performance
The software used in tube laser cutting machines allows for accurate and efficient cutting by converting 2D or 3D designs to cutting paths. The software also allows for nesting optimization, which reduces material waste and saves on costs. The software is essential in ensuring that the machines cut the tubes according to the required specifications and reduce the chances of errors.
Choosing the Right Tube Laser Cutting Machine for Your Business
When choosing a tube laser cutting machine, several factors need to be considered, including cutting speed, tube diameter, thickness, and material. Other factors include accuracy, reliability, maintenance requirements, and the cost of the machine. The choice of the machine will ultimately depend on the needs of the business and the applications it will be used for.
Conclusion
Tube laser cutting machines are essential in the manufacturing industry since they provide precise, efficient, and cost-effective solutions for cutting different metal types into various lengths and shapes. Their evolution has resulted in the incorporation of more efficient features such as automated loading, nesting optimization, and fiber-optic lasers. As the industry advances, it is likely that new developments in tube laser cutting technology will further improve the speed, accuracy, and efficiency of these machines.