Laser tube cutting is a transformative technology that utilizes high-powered lasers to precisely cut and shape hollow tubes and metal profiles. This method has revolutionized the manufacturing sector by offering unparalleled accuracy, speed, and flexibility, making it a preferred choice across various industries. Unlike traditional cutting methods that often rely on mechanical blades or saws, laser cutting employs a focused beam of light that can be finely tuned to achieve different thicknesses and materials. This capability allows manufacturers to produce complex geometries and intricate designs that would otherwise be difficult or impossible to achieve with conventional techniques. As industries continue to evolve and demand more sophisticated components, the role of laser tube cutting becomes increasingly vital.The precision offered by laser tube cutting is not merely a luxury; it is a necessity in today’s competitive market. Manufacturers are under constant pressure to improve product quality while reducing costs, and laser cutting meets these demands head-on. By minimizing the margin of error in cuts, manufacturers can ensure that parts fit together seamlessly, which is particularly crucial in sectors like automotive and aerospace, where even minor discrepancies can lead to significant safety issues. Furthermore, the ability to cut various materials—including steel, aluminum, brass, and plastics—makes laser tube cutting a versatile option for many applications. As technology progresses, we can expect even greater advancements in laser cutting capabilities, further solidifying its status as a cornerstone of modern manufacturing.

Table of Relevant Information
Category | Detalhes |
---|---|
Technology | Laser tube cutting employs lasers to achieve high precision in cutting tubes. |
Advantages | Benefits include increased speed, accuracy, and cost-effectiveness compared to traditional methods. |
Applications | Commonly used in healthcare, automotive, aerospace, construction, and more. |
Industries | Key sectors benefiting from this technology include furniture manufacturing, fitness equipment, and appliance production. |
The Mechanics of Laser Tube Cutting
Laser tube cutting machines operate through a well-defined process that begins with the preparation of the material to be cut. This involves ensuring that the tube is correctly aligned within the machine’s fixture for optimal accuracy. Once positioned, the machine’s computer numerical control (CNC) system calibrates the laser based on various parameters such as material type and thickness. This calibration is critical because different materials respond differently to laser energy; for instance, thicker metals may require more power or slower cutting speeds. The actual cutting process is where the magic happens. The laser beam moves along a predetermined path defined by CAD (Computer-Aided Design) software. As the beam strikes the material, it either melts or vaporizes it along the cut line. This process results in exceptionally clean edges with minimal burrs or roughness, significantly reducing the need for secondary finishing operations. After cutting, the sections cool down quickly due to their thin profile, allowing for immediate handling and further processing if required. The entire operation is highly efficient; modern machines can execute complex cuts at speeds reaching up to 500 inches per minute without sacrificing quality.
Advantages of Laser Tube Cutting
The advantages of laser tube cutting extend far beyond mere speed and precision; they encompass a range of factors that contribute to overall operational efficiency and cost-effectiveness. For one, the high level of precision achieved allows manufacturers to produce parts that meet stringent tolerances—often as tight as +/- 0.005 inches—ensuring that components fit together perfectly during assembly. This level of accuracy is particularly beneficial in industries such as aerospace and automotive manufacturing where safety and performance are paramount.Moreover, laser tube cutting reduces material waste significantly compared to traditional methods like sawing or punching. The focused nature of the laser beam means that less material is removed during the cutting process; this not only saves money on raw materials but also aligns with sustainability initiatives aimed at minimizing waste in manufacturing operations. Additionally, because laser machines can handle multiple shapes—round, square, rectangular—without requiring extensive retooling or setup time, they offer significant flexibility for manufacturers who need to produce various products on-demand.
Industry Applications
Laser tube cutting technology finds applications across a diverse range of industries due to its versatility and efficiency:
- Automotive Industry: In automotive manufacturing, precise cuts are essential for producing components such as exhaust systems and chassis parts. The ability to create complex shapes allows for innovations in design while maintaining structural integrity.
- Aerospace Sector: The aerospace industry relies heavily on laser tube cutting for crafting aircraft frames and engine components where precision is critical for safety and performance standards.
- Healthcare Equipment Manufacturing: Medical devices often require intricate designs made from stainless steel or other materials that benefit from laser precision. Components like surgical instruments or prosthetics are commonly manufactured using this technology.
- Construction and Building Materials: In construction, laser-cut tubes are used for structural elements like handrails or scaffolding systems where exact measurements are crucial for safety compliance.
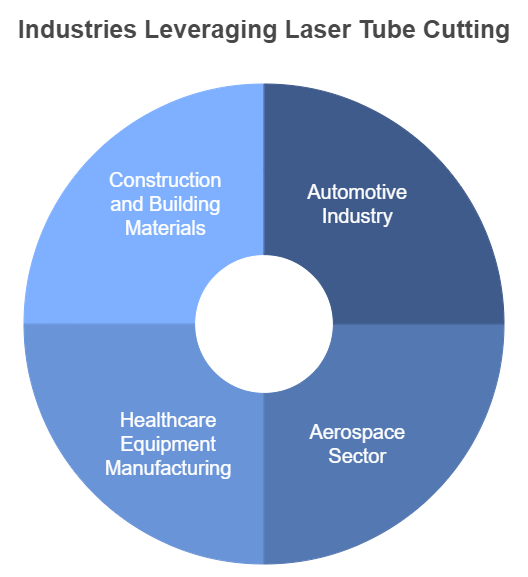
Innovations in Laser Cutting Technology
Recent advancements have significantly enhanced the capabilities of laser tube cutting systems:
- Fiber Laser Technology: Fiber lasers have emerged as a game-changer in the industry due to their efficiency and ability to cut through a wider variety of materials compared to traditional CO2 lasers. They consume less energy while providing higher-quality cuts.
- Automation and AI Integration: The integration of artificial intelligence into laser cutting machines has optimized operational efficiency by automating processes such as material handling and quality control checks. AI algorithms can analyze production data in real-time to make adjustments that improve performance.
- Advanced Cooling Systems: New cooling technologies help maintain optimal operating temperatures during extended use of laser machines. This not only enhances machine longevity but also improves cut quality by preventing overheating-related issues.
Challenges Facing Laser Tube Cutting
Despite its many advantages, laser tube cutting does face some challenges that manufacturers must navigate:
- Initial Investment Costs: The upfront costs associated with purchasing advanced laser cutting machines can be significant for smaller manufacturers or startups. While long-term savings often justify this investment through reduced operational costs and increased efficiency, obtaining financing can be a hurdle.
- Material Limitations: While laser cutting is versatile, certain materials may require specialized settings or may not be suitable for processing at all. For example, highly reflective metals like copper can pose challenges due to their tendency to reflect laser light rather than absorb it.
- Training Requirements: Operators need specialized training to effectively manage CNC systems and maintain machinery properly. This requirement can lead to increased labor costs if skilled technicians are hard to find or retain.
Future Trends in Laser Tube Cutting
The future of laser tube cutting looks promising with ongoing research aimed at improving technology:
- Sustainability Initiatives: As industries increasingly focus on sustainability practices, innovations aimed at reducing energy consumption during the cutting process are becoming more important than ever before. Manufacturers are exploring eco-friendly alternatives that minimize their carbon footprint while maintaining productivity levels.
- Customization Capabilities: Future machines may offer even greater customization options for unique projects requiring specific designs or materials. This capability will allow manufacturers to respond rapidly to market demands without compromising quality or efficiency.
- Integration with Other Technologies: Combining laser cutting with other manufacturing technologies like additive manufacturing (3D printing) could lead to new possibilities in product design and fabrication processes. Such integration would allow for hybrid manufacturing approaches that capitalize on the strengths of each method.
Conclusão
The role and status of laser tube cutting in tube processing cannot be overstated; this technology has not only streamlined manufacturing processes but has also opened new avenues for innovation across various industries. Its precision, speed, and flexibility make it an indispensable tool in modern manufacturing practices. As advancements continue to emerge within this field, we can expect laser tube cutting to play an even more significant role in shaping the future landscape of industrial fabrication methodologies.