Introdução
In the medical device industry, precision and safety are critical for the production of high-quality and effective products. Tube laser cutting machines are an essential tool in this industry, providing the ability to cut complex shapes and profiles with a high degree of accuracy and repeatability. In this article, we will explore the role of a tube laser cutting machine in medical device manufacturing, and how it is used to produce medical implants and prosthetics, surgical and dental instruments, and other medical devices. We will also discuss the benefits of using a tube laser cutting machine in the medical device industry, including improved precision, efficiency, and safety. By understanding the capabilities and limitations of a tube laser cutting machine, manufacturers can make informed decisions about the best equipment for their specific needs.
Applications in Medical Device Manufacturing
Tube laser cutting machines find extensive use in the production of various medical devices. Some notable applications include:
Catheters and Stents
The intricate designs and small dimensions of catheters and stents require high precision during manufacturing. Tube laser cutting machines can accurately cut and shape these devices, ensuring optimal performance and patient safety.
Surgical Instruments
From scalpels and forceps to surgical implants, tube laser cutting machines play a vital role in crafting precision surgical instruments. The machines’ ability to create complex geometries and sharp edges allows for the production of instruments that facilitate delicate surgical procedures.
Implants and Prosthetics
Tube laser cutting machines enable the manufacturing of implants and prosthetics with exceptional precision and customizability. By utilizing advanced scanning and measurement technologies, these machines can create patient-specific medical devices that perfectly match the anatomical requirements.
Medical Implants and Prosthetics
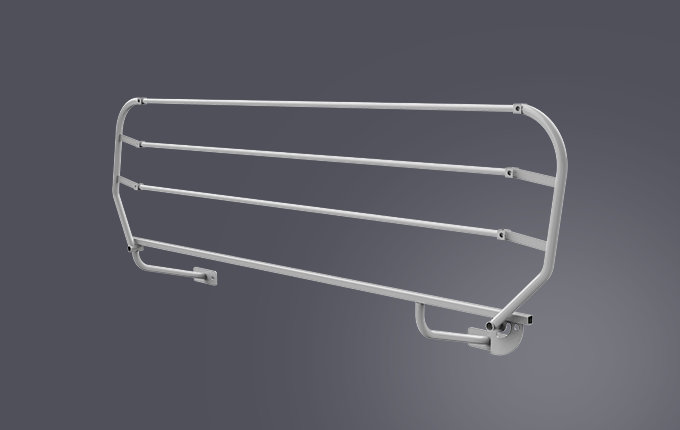
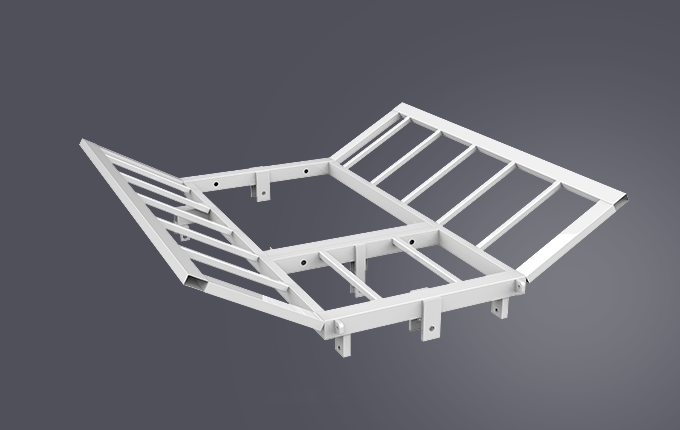
Examples of medical implants and prosthetics produced using laser cutting include:
- Orthopedic implants, such as joint replacements and spinal implants
- Dental implants, such as crowns and bridges
- Cochlear implants and other hearing aids
- Prosthetic limbs and other assistive devices
Surgical and Dental Instruments
- Orthopedic implants, such as joint replacements and spinal implants
- Dental implants, such as crowns and bridges
- Cochlear implants and other hearing aids
- Prosthetic limbs and other assistive devices
Other Medical Devices
- Surgical scissors and forceps
- Dental drills and scalpels
- Retractors and elevators
- Trocars and needle holders

Benefits of Using a Tube Laser Cutting Machine
- High precision and accuracy: Laser cutting machines are able to produce cuts with a high degree of precision and accuracy, with tolerances as low as 0.1mm. This is especially important for medical implants and prosthetics, which must be able to fit and function properly in the human body.
- Efficiency: Laser cutting is a highly efficient process that can produce parts in a short time, with minimal material waste. This can help to reduce costs and improve productivity in the medical device industry.
- Complex shapes: Laser cutting machines are able to cut complex shapes and profiles that would be difficult or impossible to produce using other methods. This allows manufacturers to produce custom devices that meet specific design requirements.
- Minimal material distortion: Laser cutting generates minimal heat, which helps to prevent warping or distortion of the material. This is especially important for medical implants and prosthetics, which must maintain their structural integrity and performance under extreme conditions.
- Versatility: Laser cutting machines can be used to cut a wide range of materials, including metals, plastics, and composites. This allows manufacturers to choose the best material for their specific application.
- Cost-effectiveness: Laser cutting can be more cost-effective than other manufacturing processes, especially for small batch production or prototyping. This makes it a good option for producing prototypes or one-off custom devices.
Challenges with Tube Laser Cutting
There are several challenges that manufacturers may face when using tube laser cutting machines, including:
Initial investment: Tube laser cutting machines can be expensive to purchase, especially if they are large or have advanced features. This can be a significant challenge for manufacturers, especially those with limited budgets or resources. Operating costs: The ongoing operating costs of a tube laser cutting machine, including the cost of the laser source, assist gas, and consumables such as lenses and nozzles, can be high. These costs can vary depending on the specific machine and the materials being cut. Material limitations: While laser cutting machines can cut a wide range of materials, there are some materials that are difficult or impossible to cut using this method. This can be a challenge for manufacturers who need to cut certain materials for their specific application. Safety concerns: Laser cutting machines can produce high-energy laser beams that can be hazardous to the operators. It is important for manufacturers to follow proper safety procedures and use appropriate protective equipment when using these machines. Maintenance and upkeep: Like any manufacturing equipment, tube laser cutting machines require regular maintenance and upkeep to ensure that they are operating at their best. This can be a challenge for manufacturers, as it requires time and resources to properly maintain the equipment.
Latest Developments & Innovations
There have been several recent developments and innovations in the field of tube laser cutting: Increased automation: Many newer tube laser cutting machines are highly automated, with features such as automatic material handling, automatic focusing, and automatic nozzle cleaning. This can help to improve efficiency and reduce the need for manual labor. Improved accuracy: Advances in laser technology have led to the development of laser sources that are more precise and accurate than ever before. This has allowed manufacturers to produce cuts with even higher levels of precision and accuracy. Enhanced cutting speed: Some newer tube laser cutting machines are able to cut at faster speeds than previous models, which can help to improve productivity and reduce costs. Improved beam quality: Improved beam quality can help to produce higher quality cuts, with less material distortion and better edge quality. Multitasking capabilities: Some tube laser cutting machines are equipped with multitasking capabilities, allowing them to perform multiple functions in a single setup. This can help to improve efficiency and reduce setup times.
Conclusão
In conclusion, tube laser cutting machines play a critical role in the medical device industry, providing the ability to cut complex shapes and profiles with a high degree of accuracy and repeatability. These machines are used to produce a wide range of medical devices, including implants and prosthetics, surgical and dental instruments, and diagnostic and monitoring equipment. The use of a tube laser cutting machine offers a number of benefits, including increased precision and accuracy, efficiency and cost-effectiveness, improved safety, and versatility. However, there are also a number of challenges that manufacturers must consider when using a tube laser cutting machine, including the initial investment, operating costs, material limitations, and safety concerns. Despite these challenges, the use of a tube laser cutting machine can provide significant benefits for the production of high-quality and effective medical devices.