Laser Cutting Smoke Hazards and Smoke Exhaust Mechanism
Laser Cutting Smoke Hazards
The smoke released when laser cutting metal plates can be roughly divided into dust and aerosols. 97% of them have a diameter of less than 5.7 μm, which means that most of the smoke can be Inhaled into the body. Depending on the cutting material and scene, other harmful substances will be produced, such as oil on the surface of the board, and very complex hydrocarbon composite gases; for example, if the surface of the board is filmed, aliphatic and olefin compounds will be released during cutting, accompanied by Distinctive odor. If the smoke and dust generated by laser cutting is not effectively captured and processed, it will harm the human body and damage the environment.
Laser cutting smoke exhaust mechanism
When laser cutting plates, a fan is generally used to draw air under the cutting surface to form a negative pressure under the cutting area and suck out the smoke and dust generated by the cutting. At present, the industry basically adopts the multi-partition method, which divides the effective cutting area into multiple groups. During cutting, it follows the actual cutting position and opens the corresponding partition air door, thereby achieving better dust removal effect. as the picture shows. According to the formula, the required air volume of the dust collector is: LP=K×3600 (5H2 +FX) VX (m3/h)
(1) In the formula: K is the selection margin coefficient, ≥1.2; H is the actual suction port Distance from the cutting position, m; FX is the partition area of the dust removal hopper, m2; VX is the wind speed at the cutting position, m/s. It can be seen from equation
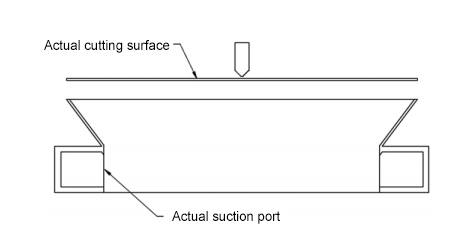
(2) that for a laser cutting machine equipped with a dust collector of the same air volume, the smaller the hopper partition area and the closer the suction port is to the cutting distance, the higher the dust removal wind speed on the workbench surface and the better the dust removal effect. After experiments with various boards and different cutting parameters, the optimal dust removal wind speed on the surface of the cutting board is 0.8~1.2m/s. At this time, the dust removal effect is good, the smoke capture success rate reaches more than 95%, and no obvious smoke can be distinguished by the naked eye; If the dust removal wind speed on the surface of the cutting plate is lower than 0.5m/s, the dust removal effect is poor, and there will be obvious smoke when cutting the carbon steel plate; if the dust removal wind speed on the cutting plate surface is higher than 1.2m/s, the dust removal effect is good and more smoke will be inhaled. Sparks or slag can cause damage to dust removal equipment and even cause fires.
Structural optimization of dust removal system
Reduce the partition area of the dust removal hopper.
From the above formula, it can be clearly seen that one of the ways to increase the dust removal wind speed at the cutting position without increasing the power of the dust collector is to reduce the partition area of the dust removal hopper.From this perspective, we conducted an actual comparative test experiment. We changed the machine tool with the same cutting format from the original 5 partitions to 6 partitions. After the improvement, the section length remained unchanged at 2.07m, and the section width was reduced from 0.85m to 0.69m, the partition area is reduced by 19%, as shown in the picture. After testing, when other conditions such as air volume, temperature, and measurement location are the same, the average wind speed on the surface of the workbench before the improvement was 0.63m/s, and after the improvement, the average wind speed increased to 0.75m/s, an increase of just about 19%. Therefore, while the air volume LP remains unchanged, reducing the partition area can directly increase the wind speed VX. However, increasing the dust removal partition will also bring some disadvantages. For example, as the number of dampers increases, air leakage points will increase; as the number of cylinders to control the dampers increases, the cost will increase, and the failure rate may become higher. Therefore, it is necessary to make choices based on the actual positioning of the product.
Reduce the distance from the suction port to the cutting surface.
It can be clearly seen from the above formula that the second method to increase the dust removal wind speed at the cutting position without increasing the power of the dust collector is to reduce the distance from the suction port to the cutting surface. surface distance. As far as the laser cutting machine is concerned, increasing the height of the air duct means shortening the distance from the air door suction port to the workbench. We also conducted a comparative test experiment. With the dust removal partition and dust removal fan unchanged, the height of the air duct was increased three times. When the H value decreases proportionally, VX continues to increase. However, due to the structure of the laser cutting machine, there are limitations to reducing the H value. In addition, the continuous improvement of the air duct also requires Consider the protection plan for the air duct to avoid laser damage. It is best to arrange the air duct outside the cutting area, especially for high-power machine tools.
Reduce the pressure loss of the dust removal system.
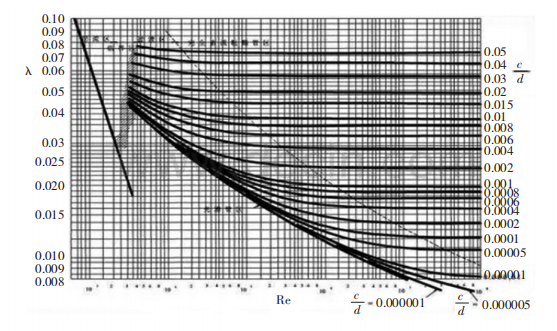
According to the Modi diagram, the damping coefficient λ along the way can be determined by the Reynolds coefficient Re and ε d (ε is the absolute roughness of the air duct wall, d is the equivalent diameter of the pipe). The larger λ, the greater the pressure along the way. The greater the loss. Combined with the actual flow of air in the air duct, it can be seen that the larger the equivalent diameter d of the air duct, the smaller λ; the smaller the inner surface area s of the tube (a certain length, the cross-sectional circumference c), the smaller the friction loss. Therefore, in terms of reducing pressure loss along the way, round tubes are preferred for air ducts, followed by square tubes and finally rectangular tubes. Under the same cross-sectional area, the equivalent diameter of the circular tube is the largest and the inner surface area of the tube is the smallest. Due to the structural limitations of the laser cutting machine, it is difficult to use round tubes as air duct structures. The main air ducts generally use square tubes and rectangular tubes; for example, 250×150 rectangular tubes and 200×200 square tubes, the equivalent diameter of the rectangular tube is 0.19m; The equivalent diameter of the square tube is 0.2m. After testing, when the length of the air duct is constant and the air volume is 5000m3/h, the unit pressure loss of the rectangular tube is 34.86Pa/m, and the unit pressure loss of the square tube is 26.93Pa/m, a decrease of 23%. The recommended value of wind speed in the air duct of the laser cutting machine is 15~18m/s. According to V=Q/S, we can check whether the selection of the air duct section is reasonable based on the air volume of the dust collector and the recommended wind speed value in the duct. If the wind speed in the pipe is too low, smoke and dust will easily accumulate in the pipe; conversely, if the wind speed in the pipe is too high, the system pressure loss will increase and the dust removal efficiency will decrease. Therefore, when selecting a dust collector, you must not only choose a dust collector with corresponding air volume, but also consider the pressure loss of the dust removal system of the laser cutting machine. The inlet air pressure of the dust collector cannot be less than the pressure loss of the dust removal system of the laser cutting machine. It needs to be provided by the manufacturer. The selection should be made according to the performance curve of the fan, and cannot be generalized based on the fan power.