Introduction
Metal fabrication is a growing sector of the manufacturing industry, driven by the need for high-precision parts, components, and products. While traditional cutting methods are still used, many metal manufacturing companies are turning to tube laser cutting machines to streamline production times and reduce costs. In this article, we will discuss the future of tube laser cutting machines, their benefits, and how automation is changing the metal fabrication industry.
Streamlining Production with Tube Laser Cutting Machines
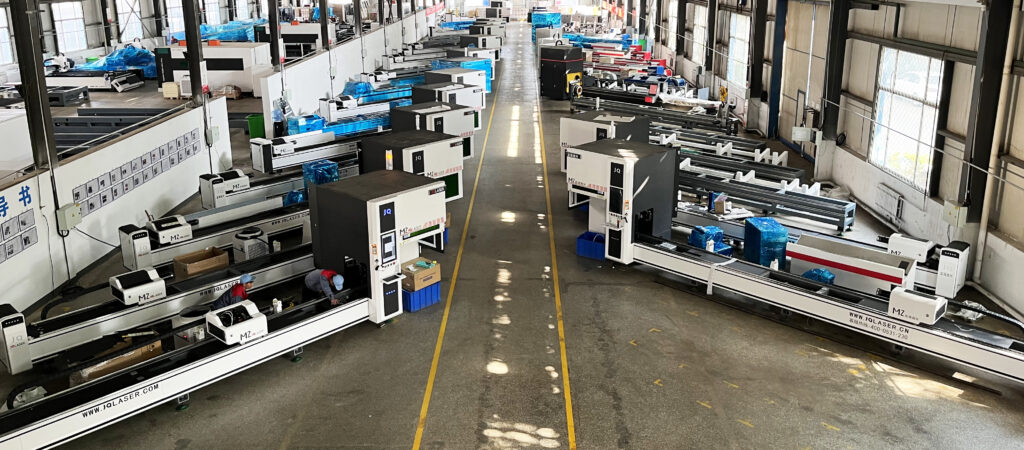
Tube laser cutting machines are revolutionizing the metal fabrication industry by streamlining manufacturing processes. These tools allow for complex shapes and designs that would otherwise be impossible to achieve with traditional cutting methods. By eliminating the need for costly and labor-intensive operations, these machines can significantly reduce production costs and delivery times. Moreover, tube laser cutting machines are incredibly efficient and energy-saving, allowing for a more sustainable production process.
The Benefits of Tube Laser Cutting Machines
Tube laser cutting machines offer a range of benefits that make them highly attractive to metal fabricators. These machines can process materials of varying thicknesses and can cut accurately along complex axes and shapes. They produce creative and intricate results that would be impossible with traditional cutting methods, making them perfect for creating highly-detailed components and products. Additionally, they are reliable, efficient, and cost-effective. As a result, they can save time and money while ensuring high-quality results every time.
The Future of Tube Laser Cutting Machinery
With the continual advancement of technology, the future of tube laser cutting machinery is bright. In the future, these tools will become increasingly automated, allowing for even faster, more efficient production processes. Advances in software will enable the machines to create complex designs and shapes with ease, meet even tighter tolerances, and produce parts with higher precision.
Unleashing the Potential of Tube Laser Cutting Machines
By utilizing the latest in automation and programming technologies, metal fabricators can unleash the full potential of tube laser cutting machines. Automation enables the machines to work at faster rates with higher precision and accuracy. Additionally, the machines can be programmed with intricate shapes and designs that would otherwise be impossible to achieve using traditional cutting methods.
How Automation is Changing the Metal Fabrication Industry
The introduction of automation into the metal fabrication industry is having a profound effect on the way that products are made. Automated tube laser cutting machines allow for the production of highly-detailed components and parts in a fraction of the time and at a fraction of the cost that it took before. This has allowed metal fabricators to achieve higher levels of efficiency and productivity, reducing wastage and eliminating costly human errors.
Identifying Advanced Laser Cutting Technology
Whilst identifying the latest in laser cutting technology can seem daunting, there are some key attributes to look for when considering which machine is best for your needs. You should look for tube laser cutting machines that offer a high beam quality, pulse length, alternating current power, and resonator frequency. Additionally, you should ensure that the machine is equipped with a fast and intuitive user interface to ensure ease of use.
The Impact of Tube Laser Cutting on Productivity
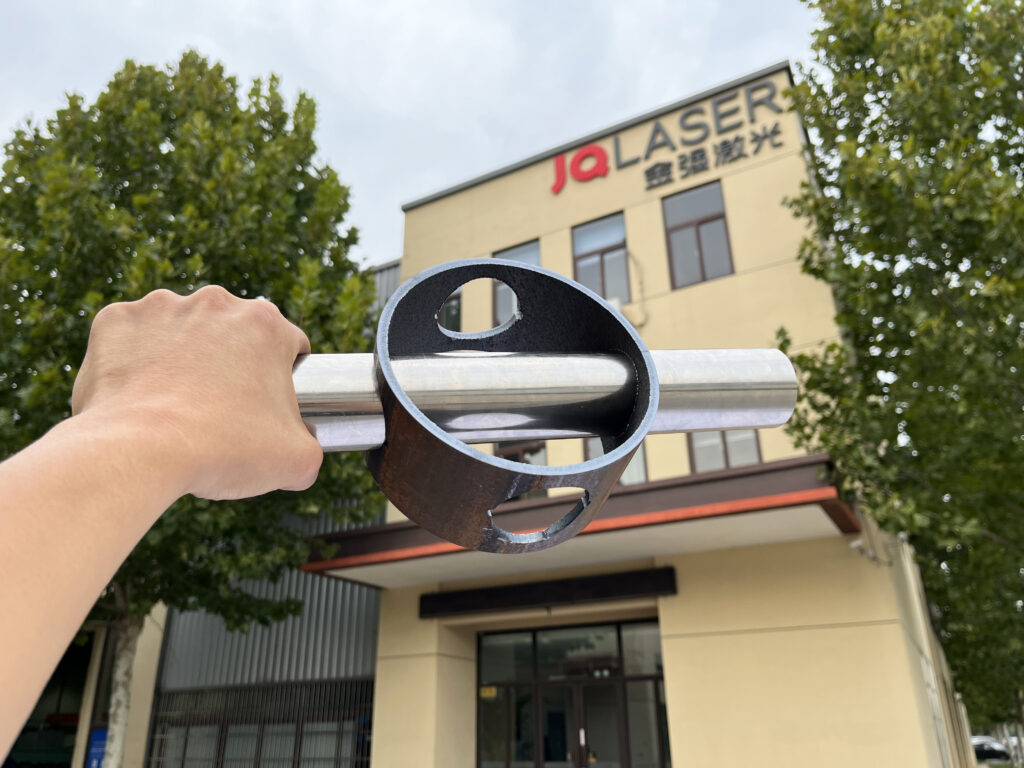
Tube laser cutting machines have had a positive impact on productivity in the metal fabrication industry. With automated tube laser cutting machines, fabricators can produce components and parts with higher accuracy and higher levels of detail at faster rates. This reduces production times and eliminates the need for expensive and labour-intensive operations, resulting in a much more efficient and cost-effective metal fabrication process.
Improving Quality with Laser Cutting Machines
In addition to improved productivity, metal fabricators can also improve quality control with the help of tube laser cutting machines. The machines can cut accurate shapes to exact dimensions, meaning that parts and components are consistent and free from human error. This ensures higher quality products that can be produced in shorter cycles, allowing metal fabricators to remain competitive in today’s market.
The Advantages of Laser Cutting Over Traditional Cutting Methods
Tube laser cutting machines offer a range of advantages over traditional cutting methods. In addition to increased accuracy and faster production times, the machines can also cut through thicker materials and tighter tolerances, producing complex shapes and designs. They are also more efficient, producing less waste and using less energy. This makes them highly cost-effective and sustainable.
Training and Skill Development for the Future Workforce
As the metal fabrication industry embraces technological transformation, the need for a skilled and adaptable workforce becomes increasingly critical. Employers must prioritize comprehensive training programs that equip employees with the necessary technical expertise and a deep understanding of modern fabrication technologies. By fostering a culture of continuous learning and professional development, businesses can ensure that their workforce remains adept at operating and maintaining sophisticated tube laser cutting machines and other advanced equipment, thereby driving long-term growth and competitiveness.
Investment and Return in the Metal Fabrication Industry
Investments in cutting-edge technologies and sustainable practices have proven to be instrumental in driving growth and fostering innovation within the metal fabrication industry. Manufacturers must strategically allocate resources to acquire state-of-the-art equipment, upgrade existing infrastructure, and implement robust quality control measures. By making informed investment decisions and focusing on delivering superior value to customers, businesses can position themselves for sustainable growth and a promising return on investment in the dynamic landscape of metal fabrication.
Collaborative Innovations and Partnerships
Collaborative innovations and strategic partnerships play a pivotal role in driving collective progress and fostering a culture of continuous innovation within the metal fabrication industry. Manufacturers, technology providers, and research institutions can collaborate to co-create cutting-edge solutions, exchange best practices, and explore new avenues for technological advancement. By fostering a collaborative ecosystem, the industry can accelerate the pace of innovation, drive market competitiveness, and deliver holistic solutions that cater to the evolving needs of diverse customer segments.
Sustainable Practices in Metal Fabrication
In response to the growing global emphasis on sustainability, the metal fabrication industry is increasingly adopting sustainable practices that promote environmental stewardship and resource conservation. Embracing energy-efficient operations, optimizing material usage, and integrating recyclable materials are some of the key initiatives undertaken by forward-thinking manufacturers. By prioritizing sustainability and corporate social responsibility, businesses can not only reduce their environmental impact but also enhance their brand reputation and appeal to environmentally conscious consumers.
Conclusion
Tube laser cutting machines are revolutionizing the metal fabrication industry. By providing unprecedented levels of accuracy and efficiency, they are streamlining manufacturing processes while reducing overall production costs. The future of tube laser cutting looks bright, as advancements in automation and software technology continue to unlock the full potential of these machines. Ultimately, with the help of these machines, metal fabricators can drastically reduce production times, improve quality control, and remain competitive in an ever-changing market.