KS120
Begin with a solid foundation

Round, square,
rectangular tubes
3D
100 kg
(15 to 120 mm)
Ailenin en küçük üyesinde teknolojinin en iyisi
The bed adopts a horizontal structure and a tube-plate welded integrated bed. The whole is annealed to eliminate internal stress. After rough machining, it is subjected to vibration aging and then fine machining, which greatly improves the rigidity and stability of the machine tool and ensures the accuracy of the machine tool.
The AC servo motor drive is controlled by the CNC system. After the motor is driven, the chuck realizes rapid and reciprocating motion in the Y direction, thereby realizing the feeding motion in the Y direction. The Y-axis rack and linear guide rails are both high-precision products, which effectively ensure the accuracy of the transmission; there are limit switches at both ends of the stroke, and hard limit devices are installed at the same time, which effectively ensures the safety of the machine tool movement; the machine tool is equipped with an automatic lubrication device, which adds lubricating oil to the moving parts of the bed at a regular and quantitative time to ensure that the moving parts run in good condition, which can increase the service life of the guide rails, gears, and racks.
Fast speed response, chuck idle speed 150m/min, acceleration 1.5G:
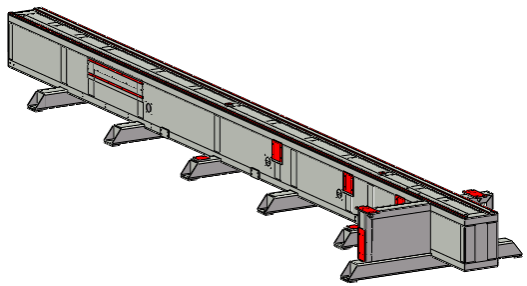
Ergonomik ve erişilebilir
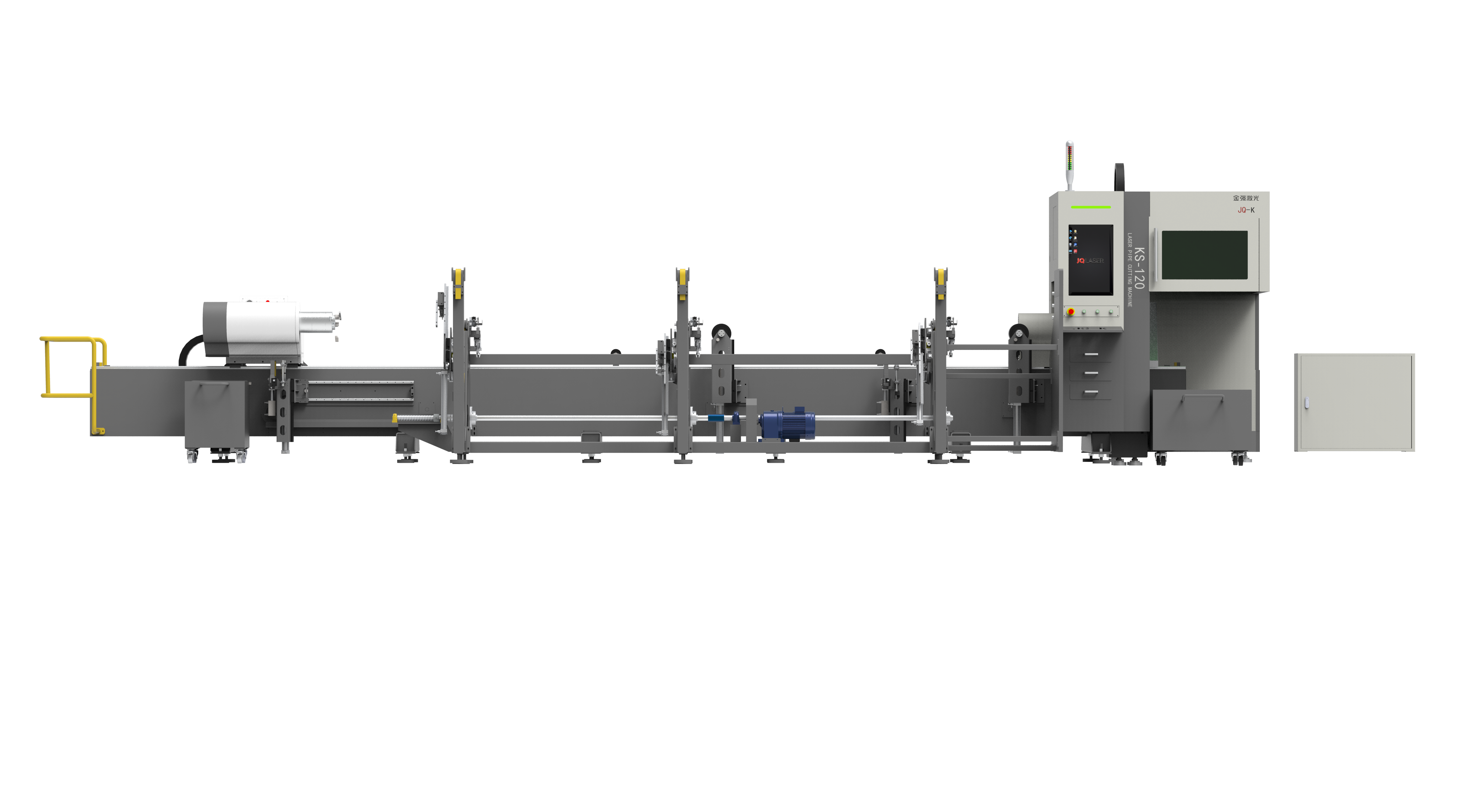
Auxiliary support and centering mechanism
The diameter scale is engraved on the variable wheel, which can be adjusted conveniently and quickly when processing pipes of different diameters, and the position can be locked after adjustment. According to the different lengths of the processed pipes, the position of the rear support can be adjusted to achieve effective support for the pipes. Within the movable distance range of the rear support centering mechanism, a length ruler is installed on the bed, which can conveniently and quickly adjust the position of the rear support, and lock the position after adjustment.

Gantry part
The gantry adopts a closed structure design of steel pipe welding. After the gantry frame is annealed to eliminate internal stress, it is roughed and finely processed to ensure that the components have sufficient rigidity and long-term stability when the laser head moves quickly, thereby ensuring the cutting accuracy.
The X-axis device is installed on the gantry beam. The X-axis is driven by a servo motor to realize the reciprocating motion of the slide in the X direction. During the movement, the limit switch controls the stroke to limit the position to ensure the safety of the system operation.
The Z-axis device mainly realizes the up and down movement of the laser head. The up and down movement of the laser head is completed by the CNC system controlling the servo motor and the motor drive module to drive the Z-axis slide to reciprocate up and down. Proximity switches are used at both ends to control the stroke to ensure the safety and reliability of the movement.
The X and Z axes are fully sealed linear modules, both of which are made of high-quality products to ensure the accuracy of the transmission.

Chuck
Under the control of the system and the action of the servo motor, the claws of the rear chuck can be kept clamped and loosened, and the pipe can be clamped and moved along the full stroke of the Y direction. The rear chuck is equipped with an independently controlled pressure regulating valve, which can adjust the chuck pressure for pipes of different wall thicknesses.
The front chuck is installed at the front end of the bed and is used to clamp the pipe for cutting. Through system control, the front chuck can be driven by the servo motor to move in a small range along the Y direction to avoid the laser head, so that short tail material can be cut under the joint clamping of the front and rear chucks. The front chuck is designed with a baffle plate and a protective cover, so that cutting dust is not easy to enter the inside of the chuck and the guide rail.
The front and rear chucks are driven by AC servo motors to achieve synchronous rotation.

Customizable feeding methods: manual, chain, fully automatic.
There are three loading methods available for selection:
- Manual loading
- Chain loading
- Fully automatic loading
Customers can choose different configurations based on their preferences. The logic and demonstration for chain loading and fully automatic loading are as follows:


Chain feeding
Fully automatic loading

En iyi seçimler zaman içinde değerini gösterir
There are 3 sets of roller support mechanisms installed on the bed. The auxiliary support is mainly for cutting longer pipes (pipes with smaller diameters).
For auxiliary control of excessive deformation, the cylinder controls the up and down movement of the support on the auxiliary support. When the rear chuck moves to the corresponding
At the position, the auxiliary support can be lowered to avoid it. For pipes of different sizes, please use the corresponding support radius to adapt to the pipe.
the height of.
Chain loading, fully automatic loading and modular docking with the host, can be added and upgraded separately later

Değer yaratan yazılım paketi
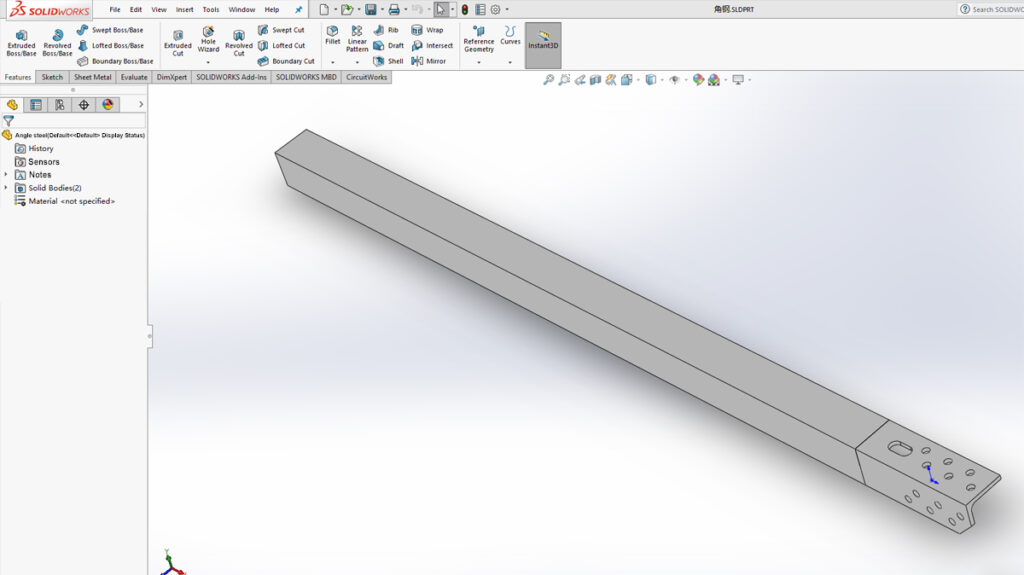
Lasertube'lerin her türlü performans marjından yararlanmak üzere tasarlanmış üç boyutlu grafik CAD/CAM ortamında parça ve çerçeve tasarımı.
Hızlandıran ve basitleştiren işlev kütüphaneleri tüp üzeri̇nde tasarim.
Ayrıntılı bir tahmin için doğru parti süresi ve maliyet tahminleri.
Uzaktan planlama ve devam eden işlerin gerçek zamanlı izlenmesi.
Tüm bunlar ve daha fazlası, her gün bir araçtan tam olarak yararlanabilmek açısından fark yaratıyor. lazer kesim sistemiverimsiz duruş sürelerini azaltır ve israfı ortadan kaldırır.
Değer seçimi aynı zamanda yazılımı da içerir.